Just got some feedback;
2 approaches
Mine is joined with a glue called resorcancal, not sure how to spell it...I just looked did up, it is spelled. " resorcinol"
Other method;
I always love an opportunity to show off my work and help someone else! Over the years I have made countless joints in boatbuilding projects using teak, mahogany and ipe using epoxy in scarf joints, some with the addition of dowels and splines. So far, 100% success. Using Acetone to wash the joint helps a lot to increase the bond strength of the adhesive but using the best possible joint structure is even more important. The more surface area of the glue joint the better, the more structure unsupported by the glue even mo better. The picture below is a dry run model showing the two joints I was planning to make in an Ipe handrail. In real life, each joint would be about 4ft apart. The right angle joint used four dowels, two in the top, two in the bottom of the rail. The angled joint used a spline. Both did well in my testing of the model below as well as the real thing that has been in service this past year and a half. Both are, essentially, butt joints so they needed dowels or splines to reduce the glue joint stresses.
Be careful in selecting the dowel or spline material. It needs to be made in the same material or of something even more durable. In your case, make the dowels from teak or spline them in teak with the grain going in the direction of the load. I made my own dowel in ipe for the corner joint and my own ipe spline for the spline joint.
Some people will likely suggest watering down your epoxy with acetone to help it soak in. This really does not prove out well in testing which I have done and is likely why West Systems does not recommend it. Mixing epoxy with acetone will help penetration but it also reduces the ultimate mechanical strength properties of the epoxy.
Make a solid mechanically strong joint, prep the surface with acetone, let it dry, slather on the epoxy full strength.
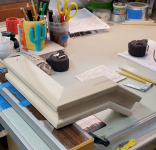