Poked away during the week, and I managed to get the transom skin cut down on the starboard side to match the PO hack job on the port side. After that I got the transom cut down to match, sanded, and drilled. There was a little bit of tear-out when drilling, but it should be fine with the aluminum pads and washers I will use on the inside for all bolts. I just eyeballed the angles and somehow managed to line up all of the holes between the motor pad, boat skin, and transom wood!
My transom wood seems a bit narrower than the tray, is that normal? It is 2 pieces of 3/4" laminated together, so I thought that would be the same as original, but I seem to have between 1/16 and 1/8" of gap. My plywood also has a few voids, what can I fill those with before sealing with OTF?
I also cut 5 of 7 floor 1/8" 1x2 angle cross braces to length and then cut in the angles so they would sit flat. I will have to cut my floor panels down in width about 6-7" to ensure they end over these braces, but then all floor seams with be directly over a brace, which I can then rivet them to.
There are a couple of holes on the transom that I need advice on. Number 1 was a PO installed bolt holding a piece of plywood for a transducer, and number 2 are the holes from an original transducer mount. I will just install a bolt to fill hole number 1 since I can't think of a good way to patch a 3/8" hole, but unfortunately when I set up my trailer for bunks they are now close to directly below the original transducer holes so I can't reuse those and risk bumping the future transducer with the bunk. To make it more complicated the holes are larger than a 3/16" rivet, so I can't just rivet them shut. Should I just drill through the transom wood and put bolts to fill those holes and then install a new transducer mount farther to the right, or should I try and reuse them but have the mount end up farther to the right?
Transom skin cut to match from the PO hack job:
Transom wood cut, sanded, and drilled:
Transom wood is narrower than expected?
What should I use to fill these voids?
Floor brace dry fit:
Old transducer holes:
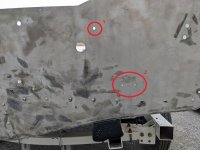