Okay an update...finally! I am continuing with the rod boxes and all the particular items that have to be installed before I can PD them in place for a final. Yes I know I am slow, but I have to think about every possible things that has to be installed before jumping in there and PBing them in place and think UH OH I screwed up! :facepalm: So I try to cover everything before that point. And usually I get it right the first install as well. Here are a few rod box pictures. NO there are not PBed because I still have a few wiring details that need to be in place first. But it is getting there.
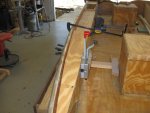
Here you can see the layout and the areas for the rod box openings.
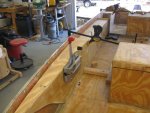
And a slight different angle. I have temporarily mounted the control box so I can get the control cables setup as to where they will run. But I also have rod PVC tubes for the rods to slide in to, and PVC tubing for the control cables and engine harness. But I also had to work the navigation rear light and courtesy lights when you open the box or storage areas. So a lot of thing that have to fit perfectly without taking away too much storage. It is getting there.
As promised before, I was also working the design of the panels I am installing in the boat. As I stated, I use a program called Visio Pro. While Visio Pro is not actually a design software program, you can actually do a lot with it once you learn about it. So I use Visio Pro for a lot of initial design work, even printed circuit board designs. So I am going to show the steps I use to make panels for the boat.
Step 1, I design the panel in Visio Pro, but seriously most any drawing programs can do this part. And I align everything up to actual sizes. That is real important when designing anything, having actual parts and components set to their actual sizes to design with. I made my own library for electronic components and that way I only have to design the sub-component once.
Here is that initial design for the read seat power outlet panel As I finished it in Visio Pro ready for transfer.
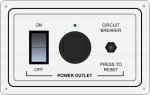
This is a screen capture directly from Visio Pro. As you can see this panel is very easy with not much going on. But they get a lot more intricate as I go on.
Step 2, after you are satisfied with the layout, you have to remove the components so you can see how the panel has to be cutout to allow the parts to be installed.
Here is that design;
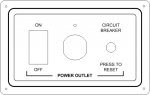
As you can see there are no parts and the design is now black and white. You actually have to change all the opening or cut out area colors to red when you transfer them to CorelDraw so the LASER will cut the openings out and raster everything that is not done in red. SO for the typical panel design you will only use two colors, being Red and Black.
Step 3, you transfer the design to CorelDraw and make all the adjustments you want before sending it to the LASER for printing. The LASER engraver only knows two things, that is Vector and Raster. Vector is the LASER cutting forms while Raster is merely LASER engraving forms. For example, if I want to cut an opening for a DPDT rocker switch like in this panel, I tell the LASER to Vector the opening. But if I want to engrave a label for that opening, then I tell the LASER to Raster that label. Sound complicated but you do those things via colors. Not hard at all. And you can easily just do your design in CorelDraw and skip the Visio Pro work. But I know Visio Pro like the back of my hand and can make a panel in mere minutes as oppose to CorelDraw taking my hours because of the learning curve. But only because I've used Visio Pro for years. So I do the initial design and transfer it. But if you are not familiar with Visio Pro, just use CorelDraw or any other Vectoring program.
Step 4, I LASER the panel out using poster board. This is actually not a needed step, but I always do this before the actual panel print just to on the safe side. When you have everything like you want, a poster board panel cost near nothing. But the actual material for the panel does cost some money. Not much, but I like to be sure.
So here is the poster board LASER panel right off the LASER engraver:
Yes it looks a little burnt, but all the parts fit and this is a lot cheaper then the panel material.
Step 5, I usually install the part to verify everything fits and works together
Here is that same poster board panel with the parts installed. Looks like everything fits just fine. Even the little green LED fits perfectly.
Step 6, Now it is time to use the real panel material for the final panel. So I select my material, in this case a horizontal brushed aluminum look, and install the material in the LASER and run it,
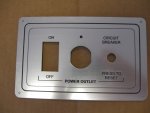
Her is the finished panel before installing the parts. Look nice to me. So let's install the parts now.
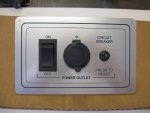
And here is the finished power outlet panel all parts installed. Not all that hard to do. Now all I have to do is finish installing this in the boat and finish the others as well.
I have four panels totally for the boat and as I get them all finished I will post them. I just wanted you all to see the many options for making your own panels. The components and panel colors and textures are endless. So design away and even if you don't have a LASER engraver, your local trophy shop does this type work all day long... Something to think about now! And a huge issue with LASER engraved panels, the print will never ever wipe away. It is engraved there forever.
Until next time, you all have a designing thoughtful day. :thumb: