Some new updates. Well today I put in a lot of hours. But sadly the pictures will not look very interest or even new because some times what you do is not going to show up in the pictures. But I have some to post anyways. I grinded all the fillets today in preparation for tabbing. Amazing how hard the Polyester Resin, Cabisol and 1/4" Milled Fiberglass strands can be when wanting to concave the fillets. I used both a 4 1/2" angle grinded with flapper disk and a pneumatic angle grinder with 2" 36 grit Rolock R disk to work the fillets over. Equally amazing is the amount of dust it creates as well. Of course I wore the respirator and eye protection, but the dust went everywhere. This grinding was inside my shop because it has been raining nearly everyday around here for a long time. In fact it was raining while I was grinding. And anybody that has ever done this before can tell you, you WILL get fiberglass splinters with both the fiberglass AND the harden poly resin. And they really do hurt...a lot. But all part of the effort. And I can tell you if you think that you can flip boats and make money, you have a better chance of selling yellow snow cones to Eskimos in the dead of winter...if you do the work correctly. Well here is the pictures;
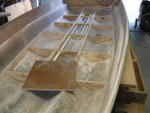
This first picture actually show the dust in the hull before I vacuumed it out. and this is the third time for that dust collection too. Hard to actually see the concave fillets. I used a piece of plywood to sit on while grinding.
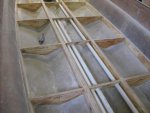
A different angle. You can see my markings to make sure each bulkhead went back to the correct place.
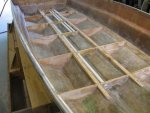
Here is the boat afer vacuuming the dust out. Really still can't see the fillets very well.
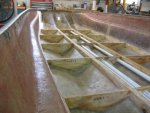
And yet another angle after vacuumed. If you look closely, you can see the bow eye support I made and PBed in place. It is absolutely solid and many times better then the original setup. If you can pull that block through the hull, you used an amazingly strong winch with the boat filled with concrete...that for sure.

Here is a closer look at the bow eye block. It is rock solid and about 1 1/2" to 2 1/2" thick as well with PB spread out over a very large area to increase the holding capability with about 7 layers of 1708 and CSM applied before the actual block itself. And then there is an aluminum backer plate too.
Well if the weather hold, I hope to tab in the all stringers and bulkhead tomorrow. Being how some of the areas are only an inch or two high off the hull, I will do the best I can with the 1708. But if it doesn't want to lay down properly, I will use CSM to finish the tabbing. I know that isn't the usual protocol, but I don't know anything else to do with such small parts. However, they will be tabbed and they are already so strong that I think you would have to use a sledge hammer to try and break them out...
Until the next time, you all have a amazing day... :thumb: