BWR1953
Admiral
- Joined
- Jan 23, 2009
- Messages
- 6,195
More progress today. Much of it a learning experience for both the boy and myself. And some lessons were painful! 
We did some more cleaning and then moved on to rib reinstallation and rivet stuff. We both had to learn about installing solid rivets, a first for us.
I showed the boy how clecos work. He was impressed... a little.
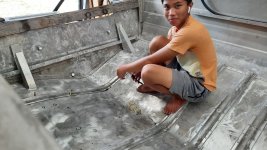
We used the JB MarineWeld to fill some of the rivet holes. We'll decide later if we want to drill them out and reuse them, or drill new holes.
We started out using the old school method of smearing the JB on, but then moved up to the syringe, which was far more effective.
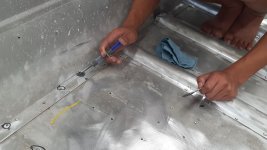
Then we moved on to riveting with the air hammer. My first result on some scrap aluminum was a large blood blister on my left index finger. And the boy got poked on the back of his hand.
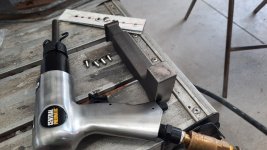
But we finally figured it out. Each of us got to install rivets correctly. We're ready to drill holes in the boat.
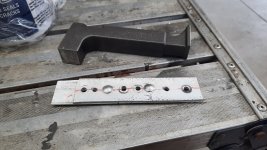
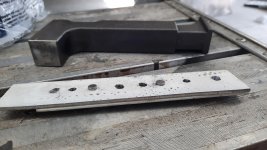
We did some more cleaning and then moved on to rib reinstallation and rivet stuff. We both had to learn about installing solid rivets, a first for us.

I showed the boy how clecos work. He was impressed... a little.

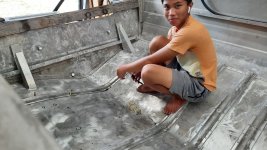
We used the JB MarineWeld to fill some of the rivet holes. We'll decide later if we want to drill them out and reuse them, or drill new holes.
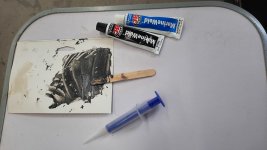
We started out using the old school method of smearing the JB on, but then moved up to the syringe, which was far more effective.
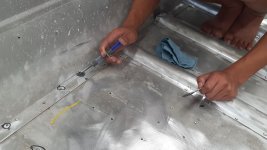
Then we moved on to riveting with the air hammer. My first result on some scrap aluminum was a large blood blister on my left index finger. And the boy got poked on the back of his hand.

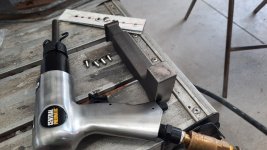
But we finally figured it out. Each of us got to install rivets correctly. We're ready to drill holes in the boat.
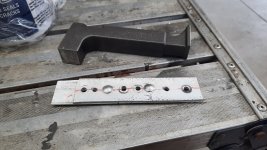
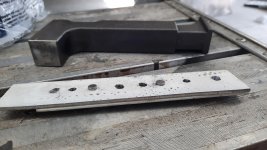