- Joined
- Jul 18, 2011
- Messages
- 18,453
Just watching football . . . Bears vs. Lions 
In terms of the height of the platform above the waterline, the existing swim platform is about 15" above the water line, so I figured dropping down the extension about 6" would provide enough height above the waterline.
Here is the model with some water added. It comes out to be about 5" clearance to the water. I'm not sure how that will play out in a getting 'out of the hole' situation :noidea:
.
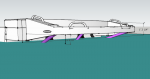
.
Back to the game
In terms of the height of the platform above the waterline, the existing swim platform is about 15" above the water line, so I figured dropping down the extension about 6" would provide enough height above the waterline.
Here is the model with some water added. It comes out to be about 5" clearance to the water. I'm not sure how that will play out in a getting 'out of the hole' situation :noidea:
.
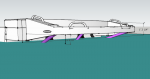
.
Back to the game