My pass-through trimming looked like it had been done by a rabid beaver.
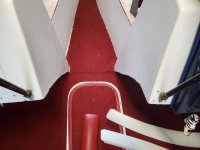
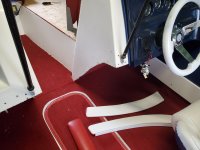
Both sides were different. Made it tricky to come up with a pattern that would work on both sides and not be huge. Happy with the end result, though.
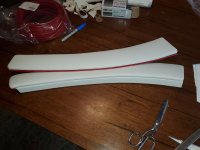
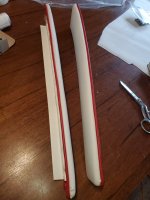
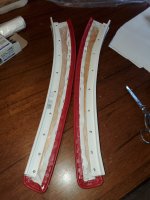
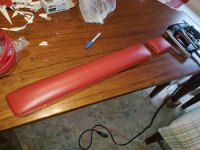
PVC corner molding caps off the raw fiberglass edges nicely. The dash pads made both sides look like they are aligned.
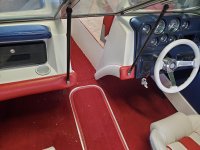
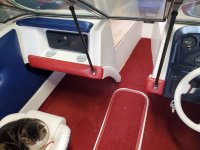
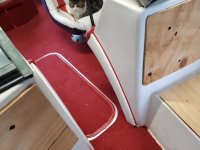
I finally go to the bow seating and worked into the evening to complete the most difficult one. It is bowed wood, with wavey stitching, at three different foam thicknesses. I dare say I bit off a little more than I could chew, but I'm rolling on with it. The opposite side is already sewn, so at least they will match.
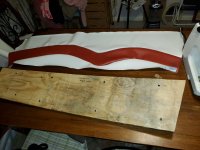
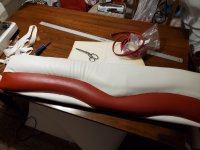
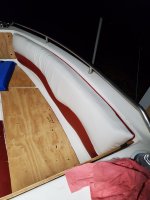
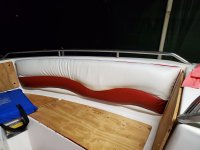
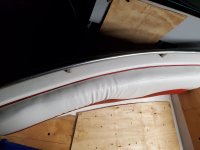
The wavey lines cause me the most trouble. If you don't get the seam allowance right, and you don't keep the seams mated accurately as you go, you get weird wrinkles that you cannot get out.
With my impaired vision, but excellent hind sight, I should have gone with a simpler design and method. But over time, vinyl will shrink and the fit will improve. I hope.
