StarTed
Senior Chief Petty Officer
- Joined
- Jul 14, 2015
- Messages
- 694
Today I spent most of my time fastening the gutters down the sides on the floor. They're sealed with 4000 and fastened with #10 SS 1/2" sheet metal screws.
Looking at the boat from the transom.
A view of the transom's 1/2 splashwell in place.
Looking at it from the rear. Clamps are in place because it is sealed with 5200 and curing above the SS motor mounting plate.
That's it for today.
Tomorrow is a day trip to Montana so maybe some more will get done on Thursday.
No luck on the grain bins and elevator leg but I have some more leads. It looks like I may have to part with some green stuff but so far I'm trying to at least break even. Getting down that elevator leg could be costly because it is so high and has lots of pipes coming down. Too high for me at this time of life.
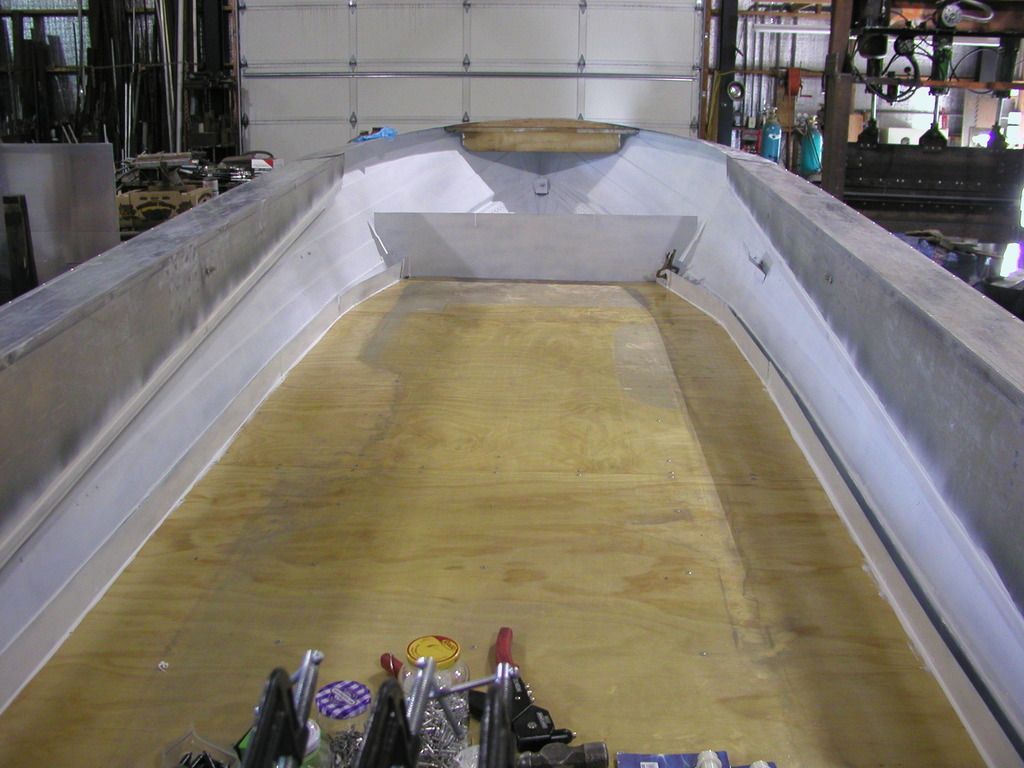
Looking at the boat from the transom.
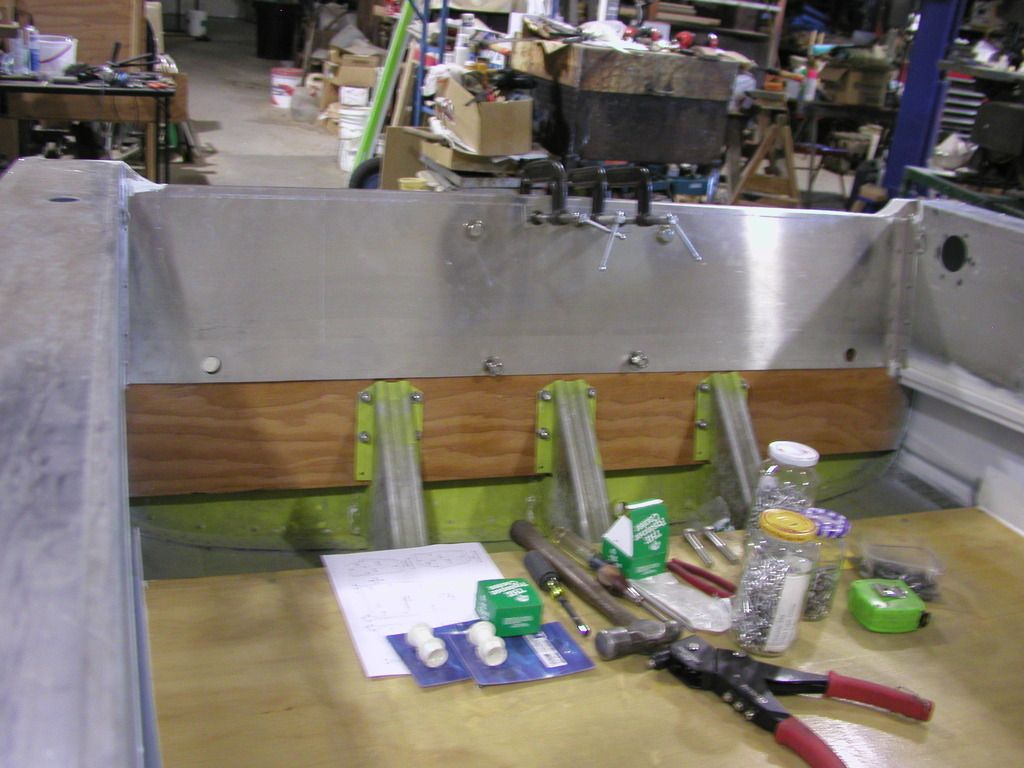
A view of the transom's 1/2 splashwell in place.
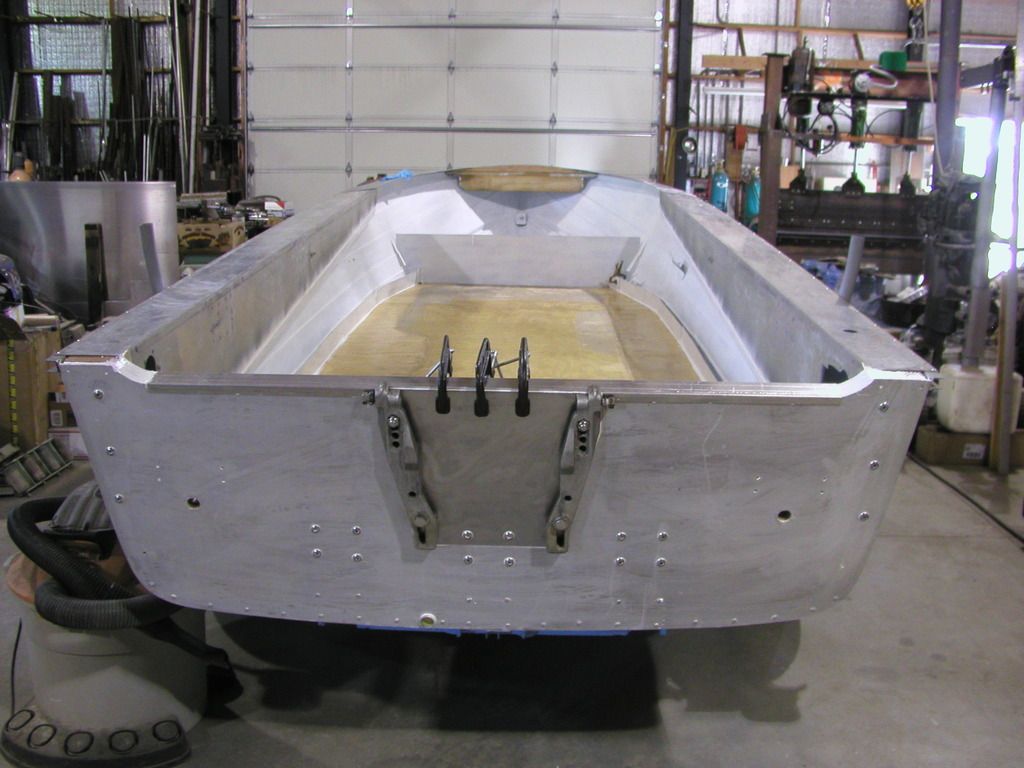
Looking at it from the rear. Clamps are in place because it is sealed with 5200 and curing above the SS motor mounting plate.
That's it for today.
Tomorrow is a day trip to Montana so maybe some more will get done on Thursday.
No luck on the grain bins and elevator leg but I have some more leads. It looks like I may have to part with some green stuff but so far I'm trying to at least break even. Getting down that elevator leg could be costly because it is so high and has lots of pipes coming down. Too high for me at this time of life.