Woodonglass
Supreme Mariner
- Joined
- Dec 29, 2009
- Messages
- 25,924
I re-read your thread and now understand the question. T-Nuts are fine as long as they're stainless. I'd use the screw in type instead of the claw foot. Another alternative is Garelick Toggle bolts They work great and are easy to use. Might consider them whichever you use I'd recommend Drilling oversized holes,filling with PB and then redrill to proper size. Seat bolt holes are notorious for leaking and damaging the wood.
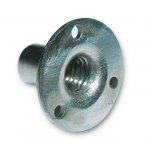
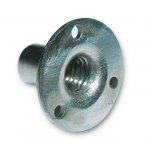