I've been having serious heartburn about flanging in a drain tube. For years. But I got it finished tonight and I'm certain it's great. Since you can never see enough pictures and tutorials, here's another one.
I started with a set of brackets milled custom to 1.040" just to fit a 1" aluminum drain pipe with O-rings. It actually wasn't expensive (at $50) and it gives me peace of mind about my old aluminum wearing out around the drain hole. Plus, I added a second hole just for a live well intake. I had them chamfer on both sides for an O-ring to match the Moeller kit. The O-ring popped right out on the straight side and I didn't have enough space after I cut to length on the existing flange side... but I had a great pocket for sealant on either side so I don't regret it.
Cut gently to 1/8-3/6" longer than the hole.
You can see the chamfer here with just a hair over 1/8" of tube past the flat portion of the bracket.
With the tool this way, I'll never flange my short tube.
This is how I solved that. Flat side to existing flange.
I didn't take any pictures of my deep well socket on the wrong side of the tool since the deep well wasn't deep enough. Turning the wrench while correcting with the socket seemed to work but I found that constant pressure on the flanged side really helped when putting it all together. I removed it when there was still a little movement in the tube, reassembled, and gave it about a half of a turn until there was no more movement in the tube.
On the inside you can see the flange follows the chamfered edge on the left hole. The O-ring popped right off onto the tool. As I used lots of 3M 4200 and the seal is tight without being cracked, I'll be shocked if it leaks around the tube.
View from the outside. 5/8" long ought to be enough to seal with a good drain plug. No extension gives me a stronger seal in my mind, so I'm going for it. As insurance I haven't knocked out the other hole which I will extend if the first one leaks and I'll put a fitting through the first hole.
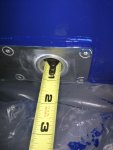