While hull work was active, the seat shells and console were also being restored. These items were fiberglass moldings with a leather like texture pattern on the outside surfaces. Starboard had painted both the seats and console but had not addressed the seat shell stress cracks that had occurred during usage.
To repair the damage to the seat shells would require significant grinding of the surfaces so new glass matt and resin could be added without significantly increasing the thickness. The repair work would result in new surfaces that would not have the texture of the originals. It was decided to make all the outside surfaces smooth. This will not be original but the new surfaces will be much easier to keep clean and will match the surface finish of the other white painted areas on the hull and covers.

Seat shell repairs involved significant rebuilding of the shell structure, filling cracks and recontouring.
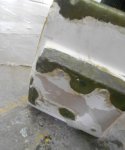
Repairs to the seat bottom.
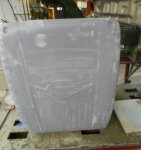
The shell back after repair, filling, and sanding.
The seat shells, as received from City Auto Body, were beautifully finished on the outside. The insides were still rough and needed sanding before a final finish was added. The bottom board was also smaller than the seat base so the loads were not distributed as widely as possible. The shells were sanded on the inside and the bottom boards replaced with new, larger items. The sides of the boards will be resin blended into the sides of the shell so there will be no recess around the perimeter of the board. This will also transfer any movement loads into the sides of the shell rather than concentrating them primarily in the bottom.
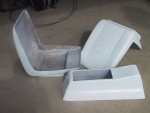
The seat shells and console as received after repair and paint.
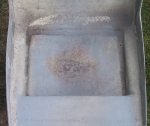
The original bottom board after repair of the mounting hole areas. Note the rough interior surfaces of the shell and the channels around the bottom board, making the seat shells hard to clean.
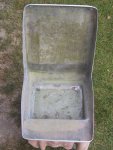
The interior of the seat shell after removal of the original bottom board and sanding of the interior surfaces.
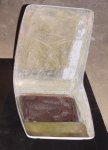
The new bottom board bonded into place. It covers the entire bottom surface to spread the loads over more area and provides a smooth bottom surface.
When riding on rough water, the forces against the seat shells are fore and aft on the backrest and vertically on the cushions. The fore/aft motions have to be resisted by the mounts on the base. This places stresses where the base and backrest join. The inside surface of the sides in these area was reinforced with a layer of thin fiberglass cloth and resin and faired into the sides.
When fitting the seat back into the shell it was noted that there is a large cavity between the seat back board and the inner shell. In case of a sinking, this volume would fill with water and contribute nothing to flotation. It was decided to add foam into this volume to assist in flotation. A calculation showed that foam could be simply added that would contribute about 10 pounds of flotation per seat. The completed foam shapes were epoxied for a smooth surface and then painted with the interior paint. The foam was attached to the rear of the backrest cushion with a few silicone dots. This will allow easy removal if desired in the future.
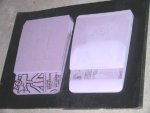
The backrest foam flotation. The left assembly has been bonded together but has not been shaped. The right assembly is shaped and is ready for epoxy coating.
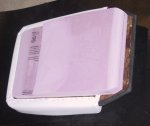
Trial fitting the flotation foam to the trimmed seat backrest. The backrest/foam assembly was also trial fitted into the seat shell to be certain that all parts would fit properly.
The backrest pad is attached to the seat shell from the rear by five screws. These screws are exposed so chrome plated trim screws with an integral cupped washer were chosen. The edges of the washer will cut into the paint so o-rings were selected to fit under the washers as a cushion.
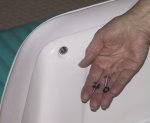
The backrest attachment screws showing how the O-rings were inserted under the trim washers to minimize paint damage from the washers.
Originally the seats were mounted with two screws, front and rear, on the centerline. This allowed the passenger seat to be reversed for observing a skier. The anchors were blind toggle type mounted to the floor. After some time the hardware corroded and the anchors tore loose when trying to remove the bolts. With only two bolts, the stresses at the holes through the seat bases caused some damage and cracking around the mounting holes.
The new design includes four mounting bolts using brass hardware because it was easily brazed to create the unique anchors and bolts. The anchors are flat plates with four holes to screw them to the floor. The bottom has a nut brazed to it. The bolts are standard slot head machine screws with a rod brazed across the head to create a type of ?wing bolt? for easy tightening by hand.
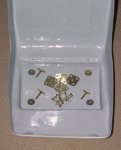
The new mounting hardware for the seats. Also note that the interiors of the seat shells have been painted to provide a good appearance and a surface that is easily cleaned.
Where the mounting bolts penetrate the seat bases, the holes are lined with short pieces of brass tubing, epoxied in place. This prevents wear on the wood bores and keeps any moisture from penetrating the wood. The tubes are shorter than the thickness of the seat base so the mounting screws will always bear on the wood base boards rather than the tubes. The washers under the mounting screws are bonded in place with silicone so they will not be a loose item to get lost.
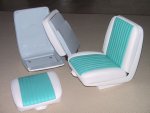
The completed seat assemblies ready for installation. The left unit shows all of the components prior to assembly. The right unit shows the final appearance of the seats. The bottom cushion of each seat is removable to access the shallow storage compartment under the cushion. As noted earlier, the backrest cushions are screwed to the seat shell and remain in place during use.