As previously mentioned, during delivery water entered the cavities under the floor and resulted in the decision to cut out the floor to be able to dry the cavities.
In retrospect, it is good that the water forced this decision. Inspection of the structure under the floor showed that the stringers were not rotted but there were other structural issues that needed correction, primarily failed bonding of fiberglass resin to wood parts so that the stringers were no longer connected solidly to the bottom of the hull. The stringers were also broken in several places where stresses were concentrated due to holes or notches. During later years of usage I noted that when hitting waves the whole structure would shake and did not feel solid. I could now see why - the floor and hull bottom were no longer well connected and could move separately in a vertical direction.
While the boat is on the cradle, the stringers will be replaced. The floor was cut out above the starboard outboard stringer forward to the floor step. The cavities were partially filled with Great Stuff foam that Starboard Marine had squirted into the spaces through floor openings per my request. The foam filled most of the volume but still left some voids where water could collect, so it is not the most effective method of adding flotation.
During floor removal some plastic sleeves containing foam balls were found in the cavities. Starboard had mentioned that they also found some of these sleeves. They were evidently placed in the floor cavities at original build as a means of providing flotation. However, the volume of foam was much too small to provide enough flotation to keep the boat afloat if swamped.
The initial construction of the fiberglass caps over the stringers was not well done and there were gaps in the fiberglass. Over time, the stringer wood had shrunk and the stringers no longer fit tightly within the fiberglass caps.
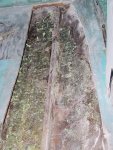
The starboard outboard stringer as originally installed.
The fiberglass cap for the stringer was cut away and the stringer removed easily as it was not bonded to the bottom. The stringer had no rot but had broken at some weak areas near the rear of the boat. The poor construction of the stringer caps would have allowed any water to get to the stringers. Probably what saved these from rot was that early on I closed the drain holes in the bilge well so water could not get into the underfloor area.
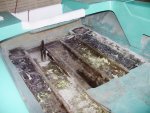
Looking aft at the crude initial installation. The loose piece at the end of the starboard inboard stringer is a portion of the fiberglass cap that was easily torn loose from the stringer and the bottom.
After removal of the stringers, the inside of the bottom was sanded smooth to remove all the old material from the fiberglass stringer caps and to provide a good surface for bonding the new stringers and the fiberglass strips that reinforce the stringer to bottom joint. The inner bottom surface was not perfectly straight so some sanding was required to get the stringer to fit reasonably well. The epoxy resin will adequately fill the remaining small gaps between the stringer and bottom.
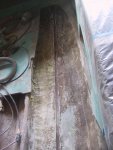
The track where the starboard outboard stringer laid on the bottom. It was not bonded to the bottom and depended only upon the fiberglass cap to provide bottom strength.
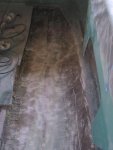
The bottom surface after grinding away all the old stringer cap material.
The wood chosen for the new stringers was clear poplar. Oak was another possibility. The outboard stringers were made from 1 X 3 and the inboard stringers from 1 X 4 finish sanded boards. Careful selection was required to get boards that were as straight as possible.
The old stringers were not usable as patterns as they were broken in a few places and did not fit the bottom contour reasonably closely. The outer stringer contour was defined by measuring from the inner bottom surface to the defined floor level at one foot intervals along the stringer location. Then the floor thickness (1/2 inch) was subtracted to find the height of the stringer at that location. These height dimensions were then transferred to the stringer board and the contour was cut.
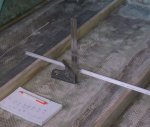
Measuring the height of the starboard inboard stringer at intervals along its length to create the contour required. The starboard outboard and port inboard stringers are shown already installed.
After consulting with a knowledgeable resin person at Jamestown Distributors, it was decided to use epoxy resin on the rebuild, even though it is more expensive and is not typically used in boat construction. It is believed that the epoxy will provide a superior bond to the various materials being used in rebuilding.
After removal of the stringer, a T-beam was placed under the stringer location on the starboard side of the hull. The port side was supported by two jack stands. The T-beam was put into place to provide a straight surface to support the bottom during fitting and bonding of the new stringer. The stringers were replaced one at a time using this method.
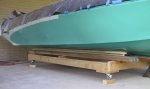
The T-beam in place under the position of the starboard outboard stringer.
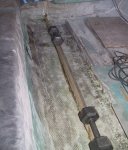
The starboard outboard stringer being bonded to the bottom. The weights were used to hold it tightly against the bottom surface while the T-beam kept everything straight.
The inner stringers went forward under the raised floor at the front of the hull. That section of floor was left in place and I did not want to remove the stringers, even though they could probably have been pulled out from under the floor. They hydrodynamic loads in that forward area are not as great as further astern so the existing structure was felt to be adequate.
The loads on the stringers are upward and by angling the cut, the loads on the new stringer will be transferred into the stub of the old stringer. To strengthen the joint between the new and old sections, small sections of ? inch plywood will be bonded to each side at the stringer joint. The fore and aft ends of these plywood pieces are ground at an angle to provide a good blend for the fiberglass cloth that will be laid along the sides of the stringer to add to the floor/stringer strength. Any gaps in the fit between the stringer ends and the plywood pieces will be filled with epoxy resin.
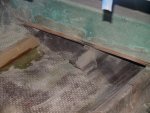
The angle cut at the end of the inboard stringers just aft of the raised floor in the bow area.
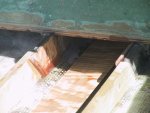
The inner plywood reinforcements at the joint between the new and old inboard stringers. Outer reinforcements will also be added and any gaps filled with epoxy resin. Also shown is the top plywood stiffener/filler for the keel channel.
Surprisingly, the hull had no keel board and depended only upon the stiffness of the hull structure to hold the keel alignment. The boat rests on keel rollers on the trailer, so it was decided to add some extra strength to the keel and also fill the channel to provide a flat area for easier fitting of the flotation foam. Strips were made from the stringer scraps, laid into the keel channel and bonded in place. The bottom layer is a narrow strip, the second layer is two wider strips, and the top layer is plywood. End joints were staggered. The side gaps will be filled with fiberglass cloth strips and resin to form a solid core for the keel channel.
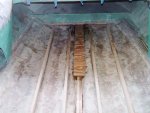
All the new stringers are bonded in place and the reinforcing strips for the keel channel are being laid into position. Cavities in the keel channel around the wood strips will be filled with epoxy resin to create a very stiff keel area.