The new reeds and needles came in, along with some needle bearing assembly grease.
The new reeds installed pretty easily on the main bearing. Still need to tighten the screws properly but turns out I don't have a socket that small for my torque wrench. :facepalm:
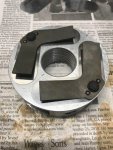
The needle bearings between the pistons and the connecting rods came together pretty easy too. Once I got the hang of the grease it held on to them nicely while I put things together.
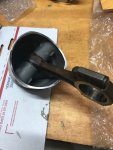
I got ahead of myself a bit and actually put the pistons on the crank shaft too.
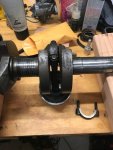
But then I realized the ring compression tool wouldn't work, so I took them back off of the crank shaft. :lol: :facepalm:
Then I tried to install the first piston into the cylinder, but it didn't go very well. I ended up snapping one of the piston rings somehow. So now I need to get a new one of those. I don't think the ring compression tool works very well. It didn't seem like I could get the rings compressed all the way. I'll have to look for something else. The tool they use in the service manual look big tongs that fit over the crank shaft and down around the piston rings.
It compresses them in two places. Unfortunately those tools are really expensive so I'd like to avoid having to get a set. I'll have to look around. I'll have to take a closer look at the one Archbuilder used too. The bore is 2.4375" so the choices don't seem that great.
But, at least I've made a little bit of progress!