Definitely HUGE move forward...
Hooked up battery + and -, now get 12.XX volts at the diode, and when I pushed on the disk the relay clicks.
Excellent!
should I hook it back up according to the wiring schematic and see if it works, or are there other things I should check first?
You could take a leap here BUT, considering the board is coming back from the grave, I'd typically approach it just a little more conservatively.
Also, I'm thinking it would be advisable to double check that all four driver FET's are still wired in parallel as per the design.
Lil background,
The high current motor driving capability of this board is quite dependent on the very low R(on) junction resistance of the FET transistors.
The manufacture's design calls for the parallel of four of the FET transistors to create theoretically an even lower effective R(on) total given by Rt(on) = 1/((1/(R1(on))+ (1/(R2(on))+ (1/(R3(on))+(1/(R4(on)))............Similar to resistors in parallel(in theory).
Although gm is a gentleman and a scholar to say the least, there might be a chance that there is a perhaps an addition disconnect lurking in the shadows.
If this is the case and a disconnect exists in the paralleled FET's config/requirement, it could cause a "situation" in that the effective R(on) will increase (see equation above less one or more R1-4(on)).
This will then causes a higher net voltage drop in the remaining paralleled FET's and at the fixed Rload (the motor), a higher voltage drop (V = IR) = more heat (P = IV) = POOF!
Given the above,
I'd recommend perhaps one or two baby steps testing solely the board up to it's limits before adding any other, although simple components, adding more variables such as switches, motors etc might overly complicate things if there are additional problems on the boards still. Suppose this way also, you'll additionally have another baseline to move up from.
As such and as it sits, I'd start by a lightly loaded test at this point which checks PWM IC and that the driver FET's are firing
1) Hook up your automotive test lamp across the J2 (motor- ) and J5 (motor+), fire it back up and push on the flex pot in various places.
2) Verify the lamp goes from dim'ish to fully lit, note that U1-2 function is to set % Duty Cycle to 100% when pressing at bottom area of flex pot on both sides of Fwd and Rev pot area's. So depending on where you've pressed the pot, It should do this (respond essentially symmetrical) on both sides of the center point......Forward and Reverse.
3) Power off, set meter to ohms, review the schmatic, check from pin #6 of U2 to the gate (pin 1 see below) of each FET for 24.3 ohms.(R17, R18, R19, R20, See post #69 schematic)
4) Check for 0'ish ohms from each FET's source (pin 3 see below) pins to ground (J4, Ground/Battery -, See post #69 schematic).
5) Check for 0'ish ohms from each FET's drain (pin 2 see below) pins to J2 (motor -, See post #69 schematic).
If all is well,
6) Replace 2'ish amp fuse with 20 amp, repeat step #1, rinse lather repeat with a headlamp bulb ( i use a hi/low beam type with both beams wired together, think that's like 55W + 65W = 120W/12V = 10 Amps).
6a) Careful, the bulb gets mighty hot, ya might want to set it such that or clamp it somehow as not to burn down the house or you.
7) Let it run on full brightness (use a paper clip or something to hold the flex pot pinched) for say a 1/2hr or so.
If she runs cold'ish still (the heat sink on the FET's), wire up the motor and switch and fire it up..............
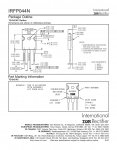