So today I started the transom patch. I read how to do it for over a week and kept bouncing back in forth with methods...I decided I just need to do it !! I am a little lucky as my stringer drive doesn't contact the transom at all, so the risk is a bit lower if I suck and did it all wrong...but here's what I did
Template cut out
Plywood fit (went through 3 plugs before I got it right....
Thought about laminating two sheets first then placing but decided against it. This method should let me take my time and hopefully do it correctly.
Went with clamps and stainless deck screws to fasten the patch to the skin. Used pilot holes to prevent cracking. Didn't coat the screws and people have said you don't want to contaminate if you plan to fill with epoxy, and if they get stuck a little soldering iron heat should loosen em up.
I used colliding silica 406 after wetting the skin side of plywood with clear/virgin resin. Once I had a mayonnaise type consistency that would stick but spread smooth I buttered up the transom skin and the wood with a small plastic floor adhesive trowel. I was liberal with the filler as I really wanted to make sure there were no airgaps if at all possible.
I used clamps and deck screws spaced
evenly and an extra transom patch to brace the skin and spread out the load.
I tightened only until the filler adhesive started to ooze out and then backed out a half turn. I did this with all clamps and then re adjusted to get even ooze out of joints...hopefully this will confirm all spots were filled.
The pressure to clamp it was fairly minimal so I didn't use another brace to spead the load on the inside. If I knock on it after curing and it sounds like an empty walnut I guess I learned my lesson.
The temperature is closer to 50 degrees tonight so im using a radiator heater in the boat with a cover to keep the Temps warmish for curing.
I used a slow hardener 206 with west systems epoxy 105 for the resin. I did not use fiberglass matting between ply and skin because I was assured through a lot of research that it is unnecessary, and the boat didn't have it from the factory.
Here's the pics. Il have a beer now and hopefully won't come back to someone telling me my boats going to blow up because I missed a HUGE IMPORTANT CRUCIAL STEP!!
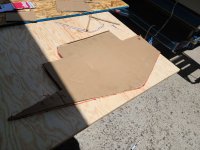
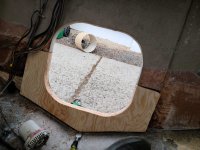
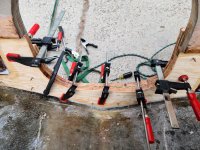
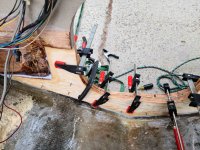
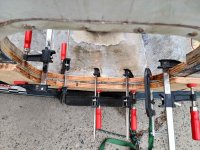
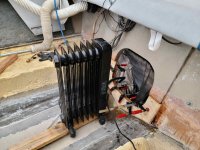