Another successful day! Couldn’t wait for an answer on the stringers so went ahead and joined then with a scarf joint 1:12 joint so about 8x8 = 64sq“ of bonding area with epoxy
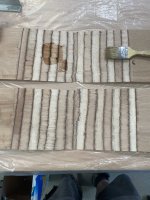
Clamped with the old favourite battery trick to get a nice ooze of epoxy out of the joint.
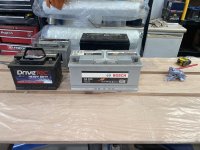
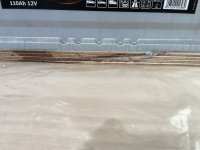
I reckon that’ll be okay bearing in mind the original was a butt joint with a 2x1 stapled on to join the wood before it was glassed together
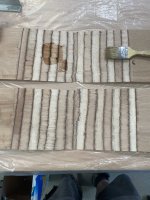
Clamped with the old favourite battery trick to get a nice ooze of epoxy out of the joint.
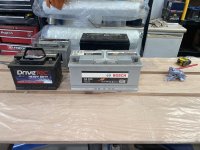
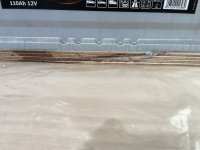
I reckon that’ll be okay bearing in mind the original was a butt joint with a 2x1 stapled on to join the wood before it was glassed together

Last edited: