markhodges78
Chief Petty Officer
- Joined
- Aug 4, 2016
- Messages
- 416
So I'm getting closer to my engine change but not there yet but have a few more question's
for starters I will not be able to do the L bracket bolt thru option because there is no access to the back side of the stringer see attached photo below. So moving on I will have to make a mount from wood so ? number 1 what should I use to fab the bed from ( 4X4 1X1 or laminate plywood together) Then after the bed is formed it gets coated with a few coats of resin and after the mount gets attached to the stringer and floor of the boat using peanut butter ? once peanut butter is cured the engine bed gets glassed to the floor and the stringer..
Is this the way it should be done...
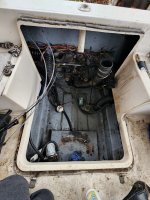
for starters I will not be able to do the L bracket bolt thru option because there is no access to the back side of the stringer see attached photo below. So moving on I will have to make a mount from wood so ? number 1 what should I use to fab the bed from ( 4X4 1X1 or laminate plywood together) Then after the bed is formed it gets coated with a few coats of resin and after the mount gets attached to the stringer and floor of the boat using peanut butter ? once peanut butter is cured the engine bed gets glassed to the floor and the stringer..
Is this the way it should be done...
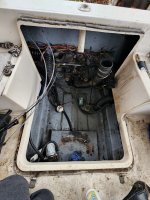