- Joined
- Jul 18, 2011
- Messages
- 18,137
I have a bunch of stuff on order to test out for the gel time reduction.
Norax MCP catalyst - extends gel time to about 2X
TBC - can be used to extend gel time 2-4 times normal by using 200 - 500 ppm. Probably best to stay 300 ppm or less.
I plan on setting up an 8" x 18" test of 3 layers of 1.5 CSM this coming weekend to see how everything will work. I will probably thin the resin by 3-5%. If my stuff arrives, I will go with the inhibitor or the Norax catalyst (but not both).
Here is a diagram of the test, showing the layers of glass and vacuum infusion/bagging materials.
Here is the planned setup, which is typical of any VARTM . . .
.
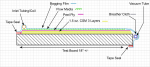
.
Here is what is supposed to happen during the infusion. . .
.
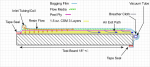
.
I plan on having the vacuum line set up so that it pulls through the fiberglass. As the resin is introduced at one end, it should flow laterally along the flow media, then downward through the peel ply into the glass layers.
This setup is typical of what the resin travel will be when I make the swim platform mold. I will time the resin travel through the flow media and then see how well the CSM is saturated.
I had been using an online resin and glass calculator, but then I realized that the resin calculation was off. It was calculating as 100% resin and no glass. I assume for hand layup there might be 80% resin 20% glass, but for vacuum bagged infusion is should be more towards 50% / 50%. Initially, the calculator showed for 1 sq. ft. of 3 layer mat, it would be about 1/8" thick, and would use 10 oz of resin. Checking the calculations, I found that the entire volume would be 10 oz. . . . so the resin is really going to be about 1/2 that.
I plan on activating 6 oz of resin for the test.
When I applied the same logic to the entire platform (42 sq. ft. x 1/8" thickness) and factor it to 50%, I comes out to only 1.7 gallons of resin for the infusion of the platform mold. Seems low, but I'll check my calc's. Based on the hatches that I infused, it seems like I have been prepping too much resin, using this calculator, as I had about 50% wasted resin. I'll plan on prepping 2 gallons of resin for the platform mold, depending on how things go with the test.
I'll post updates this comping weekend.
Norax MCP catalyst - extends gel time to about 2X
TBC - can be used to extend gel time 2-4 times normal by using 200 - 500 ppm. Probably best to stay 300 ppm or less.
I plan on setting up an 8" x 18" test of 3 layers of 1.5 CSM this coming weekend to see how everything will work. I will probably thin the resin by 3-5%. If my stuff arrives, I will go with the inhibitor or the Norax catalyst (but not both).
Here is a diagram of the test, showing the layers of glass and vacuum infusion/bagging materials.
Here is the planned setup, which is typical of any VARTM . . .
.
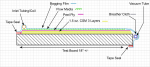
.
Here is what is supposed to happen during the infusion. . .
.
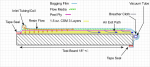
.
I plan on having the vacuum line set up so that it pulls through the fiberglass. As the resin is introduced at one end, it should flow laterally along the flow media, then downward through the peel ply into the glass layers.
This setup is typical of what the resin travel will be when I make the swim platform mold. I will time the resin travel through the flow media and then see how well the CSM is saturated.
I had been using an online resin and glass calculator, but then I realized that the resin calculation was off. It was calculating as 100% resin and no glass. I assume for hand layup there might be 80% resin 20% glass, but for vacuum bagged infusion is should be more towards 50% / 50%. Initially, the calculator showed for 1 sq. ft. of 3 layer mat, it would be about 1/8" thick, and would use 10 oz of resin. Checking the calculations, I found that the entire volume would be 10 oz. . . . so the resin is really going to be about 1/2 that.
I plan on activating 6 oz of resin for the test.
When I applied the same logic to the entire platform (42 sq. ft. x 1/8" thickness) and factor it to 50%, I comes out to only 1.7 gallons of resin for the infusion of the platform mold. Seems low, but I'll check my calc's. Based on the hatches that I infused, it seems like I have been prepping too much resin, using this calculator, as I had about 50% wasted resin. I'll plan on prepping 2 gallons of resin for the platform mold, depending on how things go with the test.
I'll post updates this comping weekend.
Last edited: