96RinkerCaptiva212
Petty Officer 3rd Class
- Joined
- Jun 4, 2017
- Messages
- 84
You won't have any problem running a ground wire from the minus tab to any convenient ground nut on the motor. The motor is well grounded.
Is that brass vent into the choke? Might be some sort of convertable heat riser fitting. I have no idea what else it might be. Too low for dumping a failed mechanical fuel pump overflow line...
If you stabbed the disty near TDC, next is to spin it up and set the timing. Can't get it much closer just by eyeballing it. Highlight your marks with chalk or white paint and you can set timing even before the motor starts. Good timing light will fire while you crank letting you nail it down.
1) Choke Fresh Air - found this diagram finally, below. Never mentions anything about hooking something up to it. Surely that thing just doesn't sit open to atmosphere with a metal screen?
2) Maybe I assumed too much with the disty cap. I now see that the previous owner had the #1 contact on the cap, pointing on the opposite of the engine away from #1 cylinder. I thought the rotor needed to be pointing at #1 cylinder on TDC and the #1 contact on the cap would be mating with the rotor (everything pointing to #1 cylinder). Is that not true? I've only had this boat for a year now so I'm not sure what all was done since '96. I can't rotate the cap 180 degrees because of this vent port on it in the 1st pic below. It is hitting the rear harness connection. So at this point, I have #1 cylinder on TDC, so I need to pull disty and drop it in so the rotor is pointing the opposite way, mating with the #1 contact on the cap? The 2nd pic shows a white paint spot on top of the cap for #1, pointing kind of towards bilge pump. This is how it was when I removed it while troubleshooting. Gosh, I'm so close and keep running into little things!! I wish I was more of a gear head!
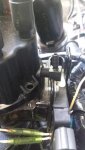
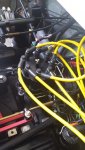