Been trying to fix some electrical gremlins.
I still haven't got to the bottom of the 'immobilser' issue but I might have fixed that anyway. To recap a marina sent the previous owner a video showing how to start the engine... turn the ignition on, then flick the cockpit light switch on/off, then turn the key to start. Originally it wouldn't start unless that procedure was followed. I took some voltage readings today, 12.6V at the key switch with ignition off but dropping to around 10V at the key switch with ignition on and around 9.9V at the ignition coil. I wondered if there was a ballast resistor fitted somewhere and if it was wired up wrong so the key switch was powered through (said) ballast resistor, but I didn't find a ballast resistor. I did find a purple wire getting warm at a crimped joint near the engine bay circuit breakers and fixed that by cutting out the crimp and soldering wires together, but the main thing I found was that the ignition switch was wired through the dead man switch (which I should have guessed) and the dead man switch had around a 1.5V voltage dtop across it with the ignition on (when supplying the ignition coil). The voltage drop due to the dead man switch was enough to see that when the key was turned to the crank position the voltage fell too low to turn the starter motor solenoid on. I have bypassed the dead man switch and now it seems to crank and start on the key every attempt.
I had already calibrated the voltmeter on the instrument cluster to show battery voltage, I now realised I should calibrate it to show voltage at the key switch because after the (above) fix it was reading higher than actual voltage. I removed and refitted the needle of the voltmeter (again) and now it shows voltage at the ignition switch accurately.
The bilge blower and bilge pump were not working, that turned out to be just due to a bit of corrosion on the fuses and fuse panel / switch panel spade connectors. They are now working properly. The bilge pump did work in automatic mode (from float signal) even before I did this fix.
Removed the sub/bass speaker cabinet from the cabin. Heh, for the time being there is a 12" hole from the driver position (near drivers legs) through into the cabin where the speaker was fitted. I might get aorund to filling that hole with something but in the short term I'll just refit the 12" speaker in the hole.
I set the number of cylinders selector on the rear of the instrument cluster to what I thought could be the 8 cylinder position but the revcounter still seems to be reading high (judging rpm by ear). I will attach a discrete digital revounter to check the accuracy of the instrument cluster revcounter.
Pictures of poor crimped connection of the purple wire in the engine bay. After taking the pictured I removed the crimp and soldered the wire together.
12V feed from engine bay (thick pink wire) goes through the discrete fuse holder, purple wire from discrete fuse holder goes to dead man switch, another purple wire comes back from the dead man switch to feed the key switch. After taking the pic I connected the pink wire directly to the key switch, bypassing the dead man switch.
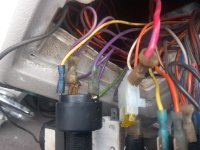