Broaters
Petty Officer 2nd Class
- Joined
- Jul 31, 2017
- Messages
- 139
Time for the seat bases to go in.
we wanted to glue them after the complete glassjob of the floor with the idea to create a uniform barrier between the seats wood and the deck wood. it was not done like this from factory but we considered it a reasonable upgrade on a durability standpoint.
We used PB to glue the seat bases as we were out of polyester glue paste. we did the filleting at the same time and come with the biax tape to tab it as the PB was still fresh. It worked pretty well and avoided the painful phase of regrinding the PB edges before glassing.
I don't know if you guys managed to do it but each time we are doing PB filets and let them cure we always ends up with Sharpe edges or weird spots that need to be grinder before glassing.
as the floor was still tacky from the covering we used cardboard sheets to walk on.
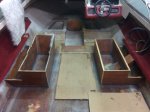
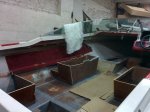
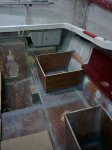
We have reproduced the same pattern for the seat base except for the opening on the 2 front seats that we will do with some hatches later on
we wanted to glue them after the complete glassjob of the floor with the idea to create a uniform barrier between the seats wood and the deck wood. it was not done like this from factory but we considered it a reasonable upgrade on a durability standpoint.
We used PB to glue the seat bases as we were out of polyester glue paste. we did the filleting at the same time and come with the biax tape to tab it as the PB was still fresh. It worked pretty well and avoided the painful phase of regrinding the PB edges before glassing.
I don't know if you guys managed to do it but each time we are doing PB filets and let them cure we always ends up with Sharpe edges or weird spots that need to be grinder before glassing.
as the floor was still tacky from the covering we used cardboard sheets to walk on.
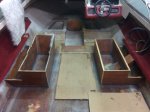
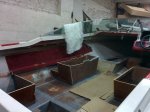
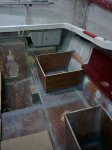
We have reproduced the same pattern for the seat base except for the opening on the 2 front seats that we will do with some hatches later on