T748
Seaman
- Joined
- May 1, 2012
- Messages
- 60
Re: 1977 Bayliner 2550
Back in post #21 I stated that the stringers were good to go. Well, on further review, that's just not true. I've been prepping the transom for removal and in doing that I needed to cut the stringers back a foot or so. Here is a picture of one of the inner stringers. It's a 2X6 That had 5/8" plywood stapled and fiber glassed to it's inner side. The plywood makes up the sides of the foam box.
Holes were drilled next to existing holes. The wood came out of the drilled holes dry light colored. I was surprised to find the stringer looked like this once removed.
It looks like the lack of proper sealing on the plywood led to rot on the back side of the stringer. Needless to say plans have been changed and all stringers will be replaced. -Tom.
Back in post #21 I stated that the stringers were good to go. Well, on further review, that's just not true. I've been prepping the transom for removal and in doing that I needed to cut the stringers back a foot or so. Here is a picture of one of the inner stringers. It's a 2X6 That had 5/8" plywood stapled and fiber glassed to it's inner side. The plywood makes up the sides of the foam box.
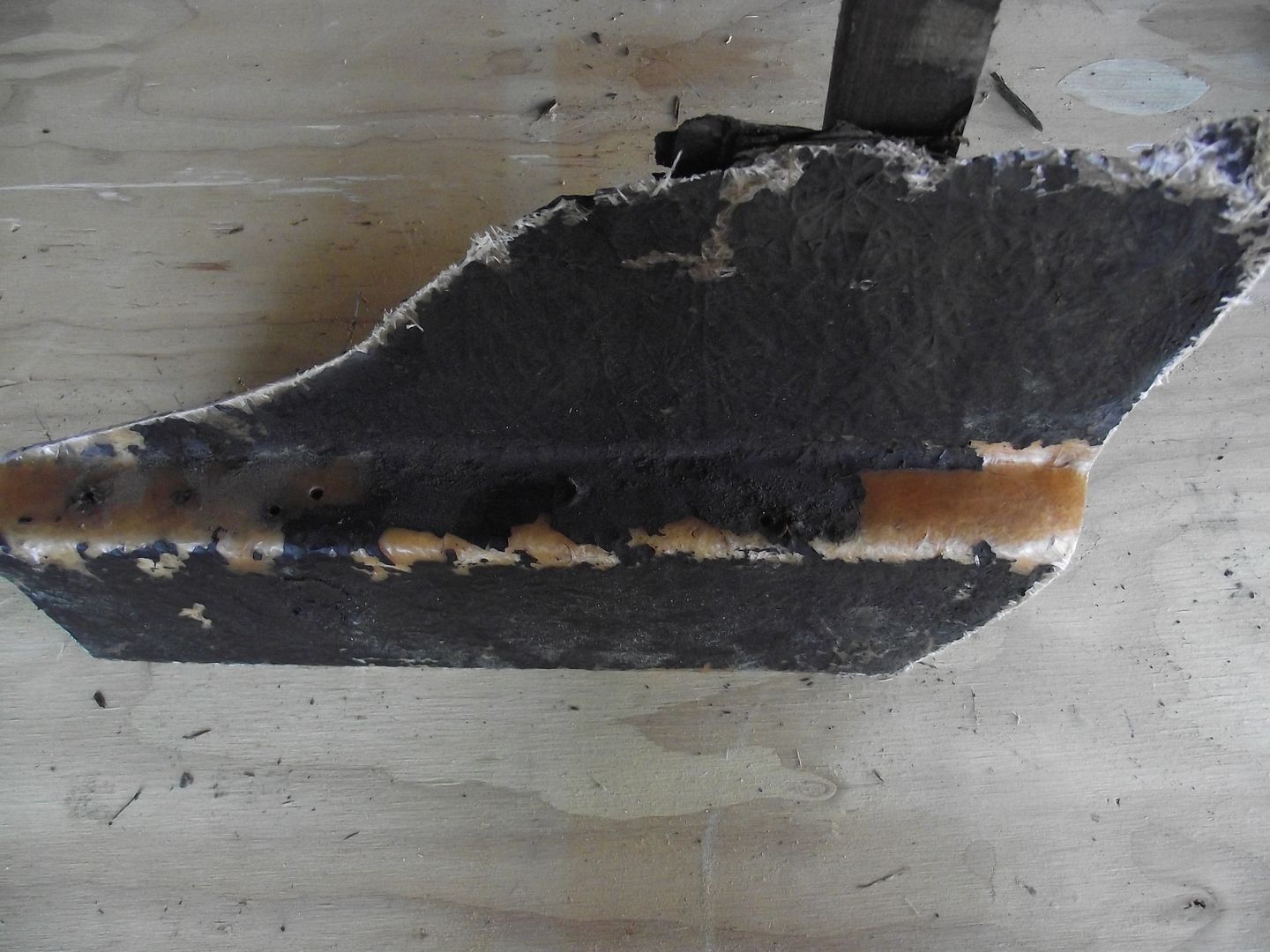
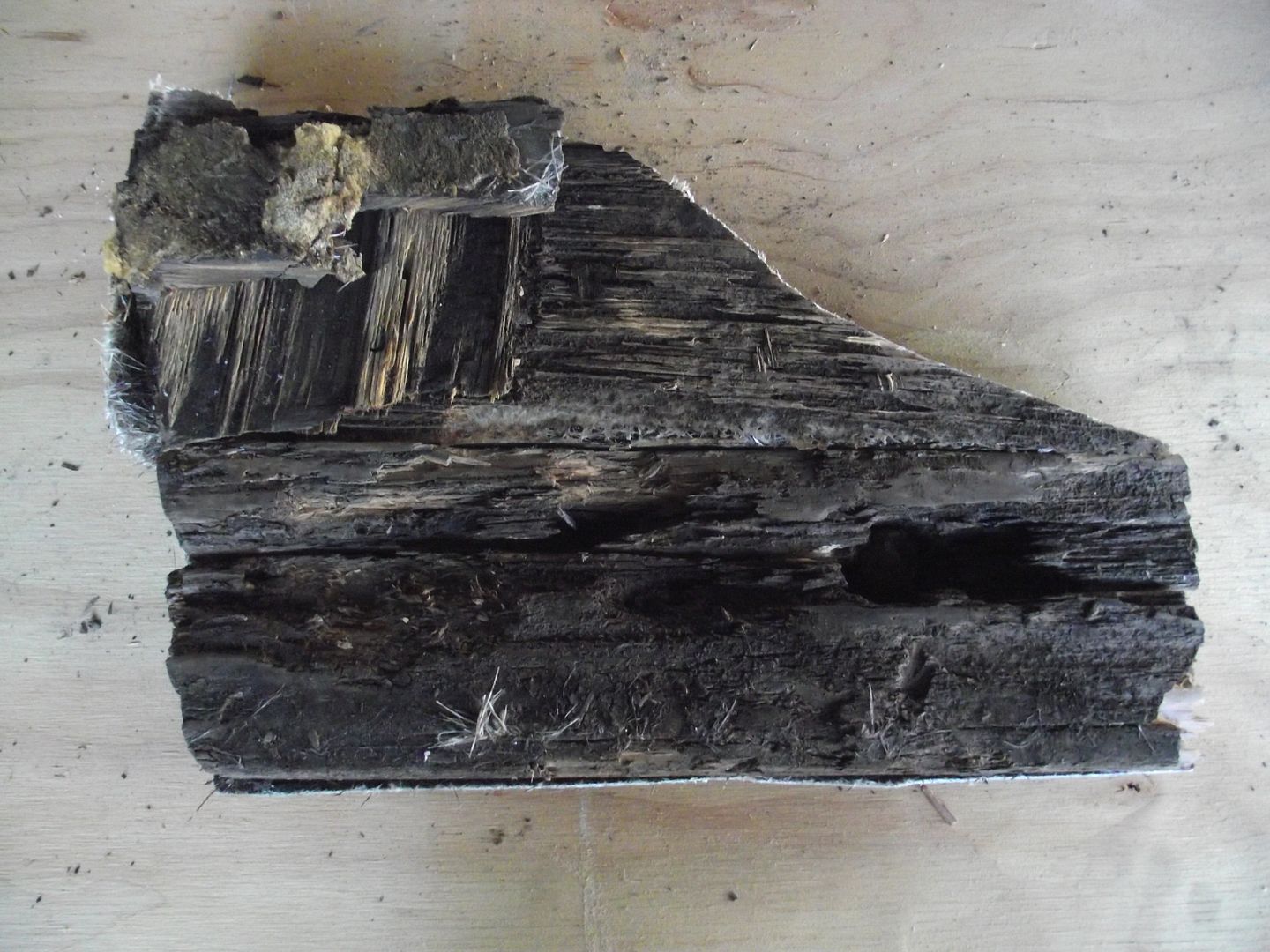
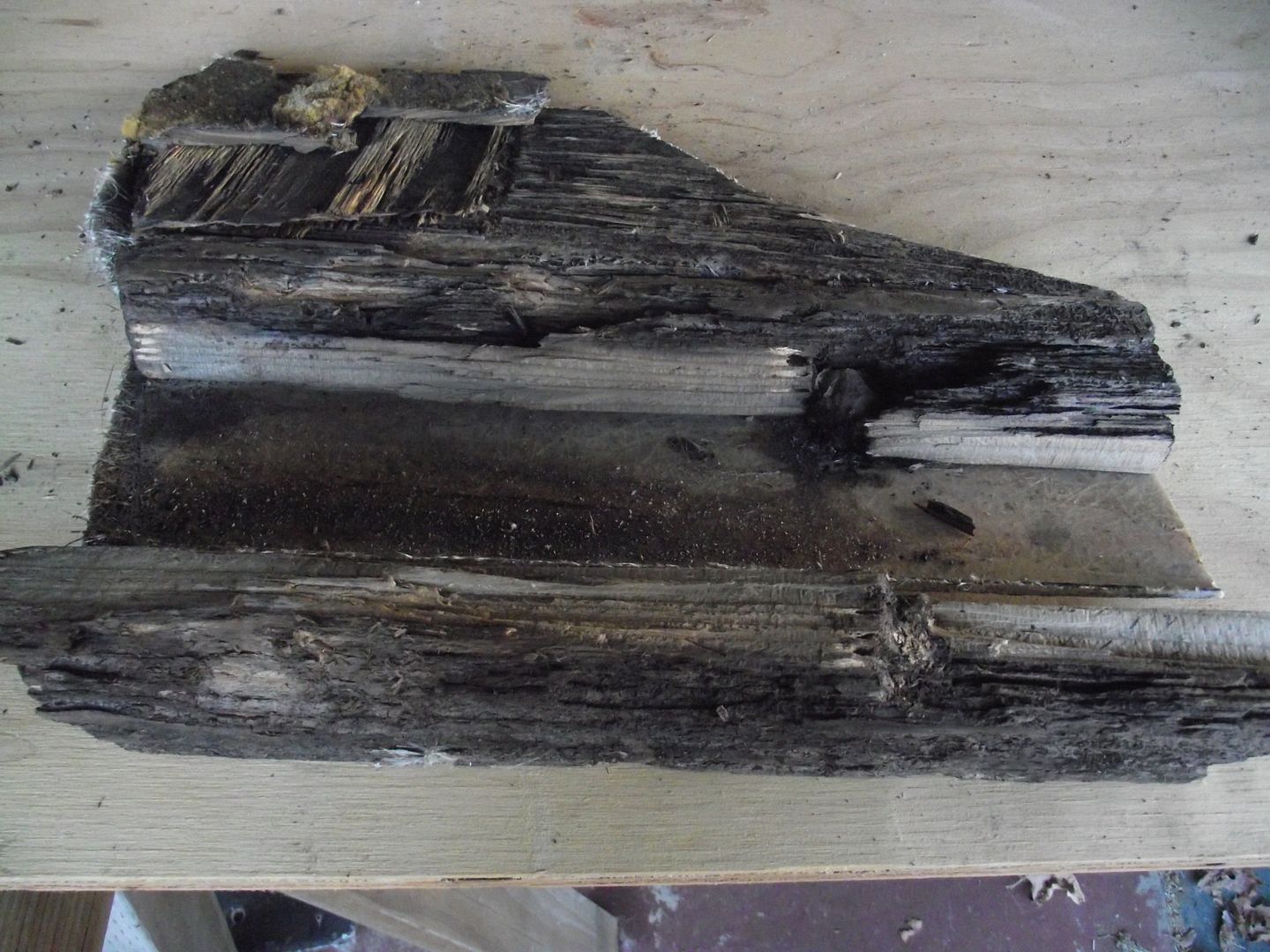