Gary H NC
Fleet Admiral
- Joined
- Dec 1, 2005
- Messages
- 8,972
I thought i would give my opinions and tips on my recent repair job.
Tools i found useful,
1- die grinder
2-chainsaw (the bigger the better)
3-wood paddle drill bits( eats up rotten wood and helps the chainsaw blade)
4-a piece of flat steel about 4 foot long,bent a little at one end and sharpened.
5- big pry bar
6-1 1/2 inch brass wire brush wheel welded to a steel rod that fits in the drill
7-Large electric drill for mixing
8-Shop-vac
Ok, a run down on how the job went.This is how i would tell someone to go about it.
I started by cutting the cap off the transom with the grinder and a thin cutting wheel.Cutting down from the top so i keep the original height and shape.
Opened it up and could see the rotted mess!
Carefully not to drill to deep take the paddle bit and drill holes about 1 inch apart.
Then the fun begins! Fire up the chainsaw and go at it.Be careful!! You can hear if you hit fiberglass so listen.
Get all you can with the chainsaw then start cleaning out the chips with the vacuum. Now the tedious part begins.Take the flat steel bar and start peeling the wood away from the outer skin.The pry bar can help here too.
This is the worst part so plan on sore hands and skinned knuckles.
When all the wood is removed take the brass wire brush wheel on the drill and clean the inner walls.This is important to scuff all this up and get all the wood particles out.
Ok,all the wood is gone.Take acetone and wash it all down.
Now to get ready to pour.
Tape all holes shut with duct tape and tape them good.
Any thru hull drain tubes can be taped into the holes,(you will pull them back out after a couple hours of the cure time)
Tape anything shut you don't want the seacast to ooze out of.
Make sure the transom is square and in the correct shape.Put a straight edge on it and check everything. A rotted transom will sag back and will have a bend in the fiberglass so fix that before the pour!
Mix the Seacast per directions,Mix it very well!! Add the fiberglass shreds slowly to it or your drill won't be able to handle it.Mix,mix and mix some more. You have a good hour before it starts to set up.
Mix one bucket at a time!
I used a V shaped home made funnel about 2 foot wide i made from scrap wood.
Start pouring it in. Have a second person using a wood dowl and working the seacast down to the bottom.Have them also to keep tapping the outside with a rubber hammer to release air pockets.
When you get about 4 inches from the top take the woven roving and tuck it in one side then fill the rest of the way.Fold the roving over the top and tuck it into the seacast. This gives it way more strength at the stress points on the transom.
About 2 hours into the cure time you will notice this stuff is cooking about 175 degrees.
To do my risers i let the bottom setup a couple hours and cool down some.Then took pieces of wood and clamped them in place leaving just enough room at the top to get a plastic funnel in there.Take the wood dowl and push the Seacast thru the funnel to get it as full as possible.
Wait for it to start cooking then remove the wood before it cures.
The small area at the very top where it did not reach i used some Evercoat Tiger hair fiberglass filler.I also used it to fill any small voids along the top of the transom.It seemed to bond very well to the Seacast.
Let it cure a couple days. Any spills you can clean up with acetone.
Install any thru hull hardware or drains using 3M sealant.
The finished product.....
Tools i found useful,
1- die grinder
2-chainsaw (the bigger the better)
3-wood paddle drill bits( eats up rotten wood and helps the chainsaw blade)
4-a piece of flat steel about 4 foot long,bent a little at one end and sharpened.
5- big pry bar
6-1 1/2 inch brass wire brush wheel welded to a steel rod that fits in the drill
7-Large electric drill for mixing
8-Shop-vac
Ok, a run down on how the job went.This is how i would tell someone to go about it.
I started by cutting the cap off the transom with the grinder and a thin cutting wheel.Cutting down from the top so i keep the original height and shape.
Opened it up and could see the rotted mess!
Carefully not to drill to deep take the paddle bit and drill holes about 1 inch apart.
Then the fun begins! Fire up the chainsaw and go at it.Be careful!! You can hear if you hit fiberglass so listen.
Get all you can with the chainsaw then start cleaning out the chips with the vacuum. Now the tedious part begins.Take the flat steel bar and start peeling the wood away from the outer skin.The pry bar can help here too.
This is the worst part so plan on sore hands and skinned knuckles.
When all the wood is removed take the brass wire brush wheel on the drill and clean the inner walls.This is important to scuff all this up and get all the wood particles out.
Ok,all the wood is gone.Take acetone and wash it all down.
Now to get ready to pour.
Tape all holes shut with duct tape and tape them good.
Any thru hull drain tubes can be taped into the holes,(you will pull them back out after a couple hours of the cure time)
Tape anything shut you don't want the seacast to ooze out of.
Make sure the transom is square and in the correct shape.Put a straight edge on it and check everything. A rotted transom will sag back and will have a bend in the fiberglass so fix that before the pour!
Mix the Seacast per directions,Mix it very well!! Add the fiberglass shreds slowly to it or your drill won't be able to handle it.Mix,mix and mix some more. You have a good hour before it starts to set up.
Mix one bucket at a time!
I used a V shaped home made funnel about 2 foot wide i made from scrap wood.
Start pouring it in. Have a second person using a wood dowl and working the seacast down to the bottom.Have them also to keep tapping the outside with a rubber hammer to release air pockets.
When you get about 4 inches from the top take the woven roving and tuck it in one side then fill the rest of the way.Fold the roving over the top and tuck it into the seacast. This gives it way more strength at the stress points on the transom.
About 2 hours into the cure time you will notice this stuff is cooking about 175 degrees.
To do my risers i let the bottom setup a couple hours and cool down some.Then took pieces of wood and clamped them in place leaving just enough room at the top to get a plastic funnel in there.Take the wood dowl and push the Seacast thru the funnel to get it as full as possible.
Wait for it to start cooking then remove the wood before it cures.
The small area at the very top where it did not reach i used some Evercoat Tiger hair fiberglass filler.I also used it to fill any small voids along the top of the transom.It seemed to bond very well to the Seacast.
Let it cure a couple days. Any spills you can clean up with acetone.
Install any thru hull hardware or drains using 3M sealant.
The finished product.....
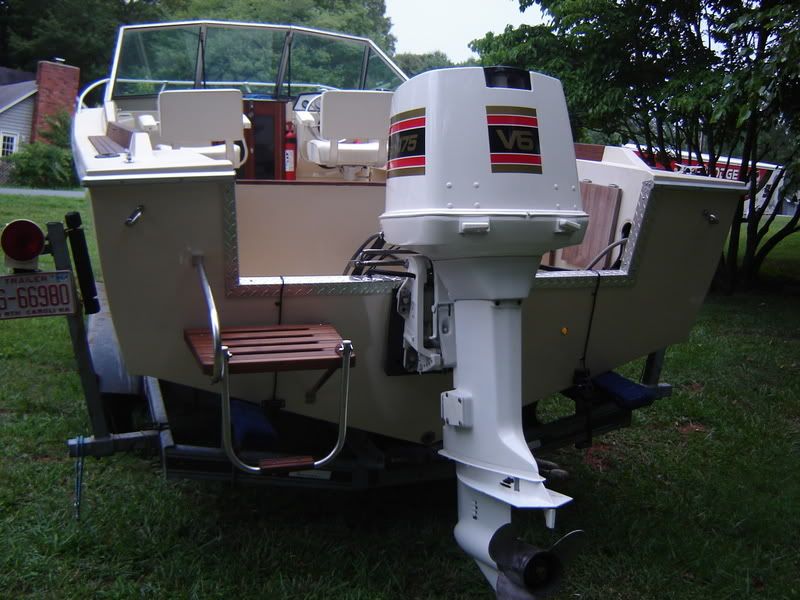