ScrewPull
Cadet
- Joined
- Jun 15, 2012
- Messages
- 17
I have been doing some light restoration work on my 1979 MasterCraft Stars & Stripes. While waiting for a swim deck bracket to be made, I decided to inspect the fiber-glass covered wooden mounting plate that's beneath the Rudder Log Plate. The glass matting looked delaminated at the forward section of the plate, so I knew I was in for a fun little project.
As I suspected, the wood beneath the glass was pretty well compromised. Glad I decided to look into it, although I've created a rather large bag of questions that need answering. I've tried getting answers at my MC forum, but haven't gotten anything. This forum seems to be far more comprehensive, so I am hoping I can get the answers I need here.
The questions I have are as follows:
1. In replacing the square, wooden plate, what is the best kind of wood to use? I am sure some kind of marine grade ply would suffice.
2. In relation to question number two, what is the best resin to use? I have some West Marine Boater's Polyester Resin and some West Epoxy Resin (105, with 206 Hardener and some 404 High Density Adhesive Filler). I also have glass matting.
3. Also in relation to question 2, can I use another substrate for the plate? I have some thick Star Board that would appear tobe a great alternative, but I want to make sure it will adhere to the resin and fiberglass. That said, would my choice of resin be different if using star board rather than wood?
4. I need to know what the proper approach is to getting the rudder alignment correct. I have searched high and low and have yet to find anything on proper rudder installation. Can anyone help with this?
The red arrows below point to the forward two corners of the glassed-over wooden plate.
Nice stuff!
Cleaned up the area a bit.
Any help would be greatly appreciated!! Thanks!
As I suspected, the wood beneath the glass was pretty well compromised. Glad I decided to look into it, although I've created a rather large bag of questions that need answering. I've tried getting answers at my MC forum, but haven't gotten anything. This forum seems to be far more comprehensive, so I am hoping I can get the answers I need here.
The questions I have are as follows:
1. In replacing the square, wooden plate, what is the best kind of wood to use? I am sure some kind of marine grade ply would suffice.
2. In relation to question number two, what is the best resin to use? I have some West Marine Boater's Polyester Resin and some West Epoxy Resin (105, with 206 Hardener and some 404 High Density Adhesive Filler). I also have glass matting.
3. Also in relation to question 2, can I use another substrate for the plate? I have some thick Star Board that would appear tobe a great alternative, but I want to make sure it will adhere to the resin and fiberglass. That said, would my choice of resin be different if using star board rather than wood?
4. I need to know what the proper approach is to getting the rudder alignment correct. I have searched high and low and have yet to find anything on proper rudder installation. Can anyone help with this?
The red arrows below point to the forward two corners of the glassed-over wooden plate.
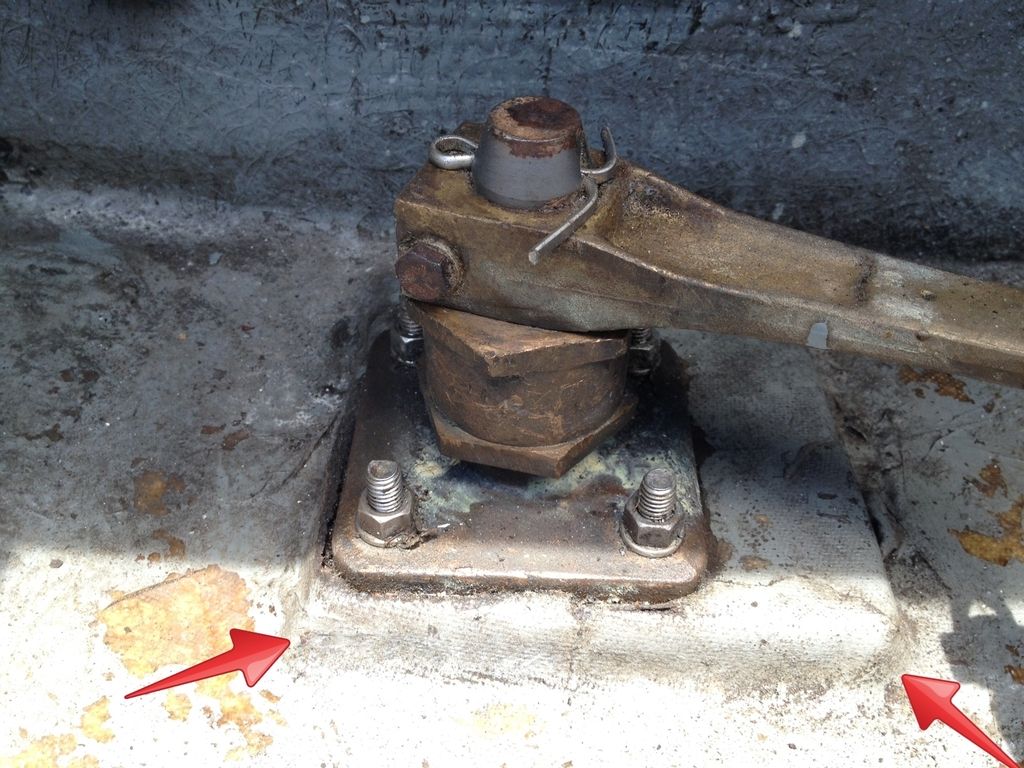
Nice stuff!
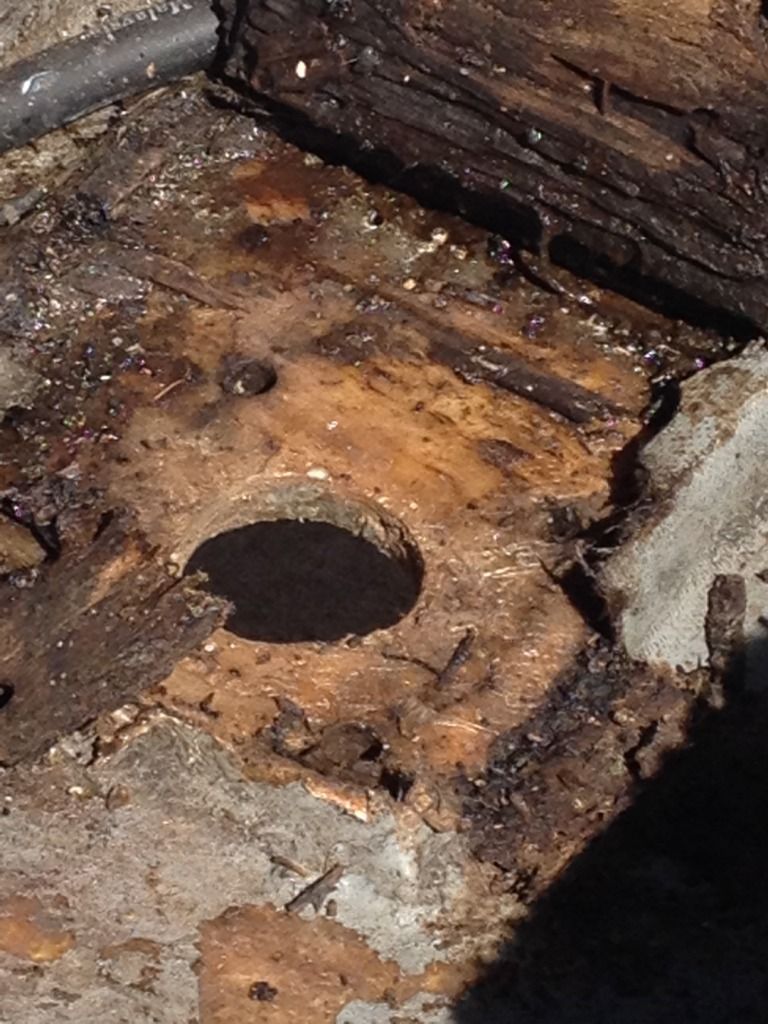
Cleaned up the area a bit.
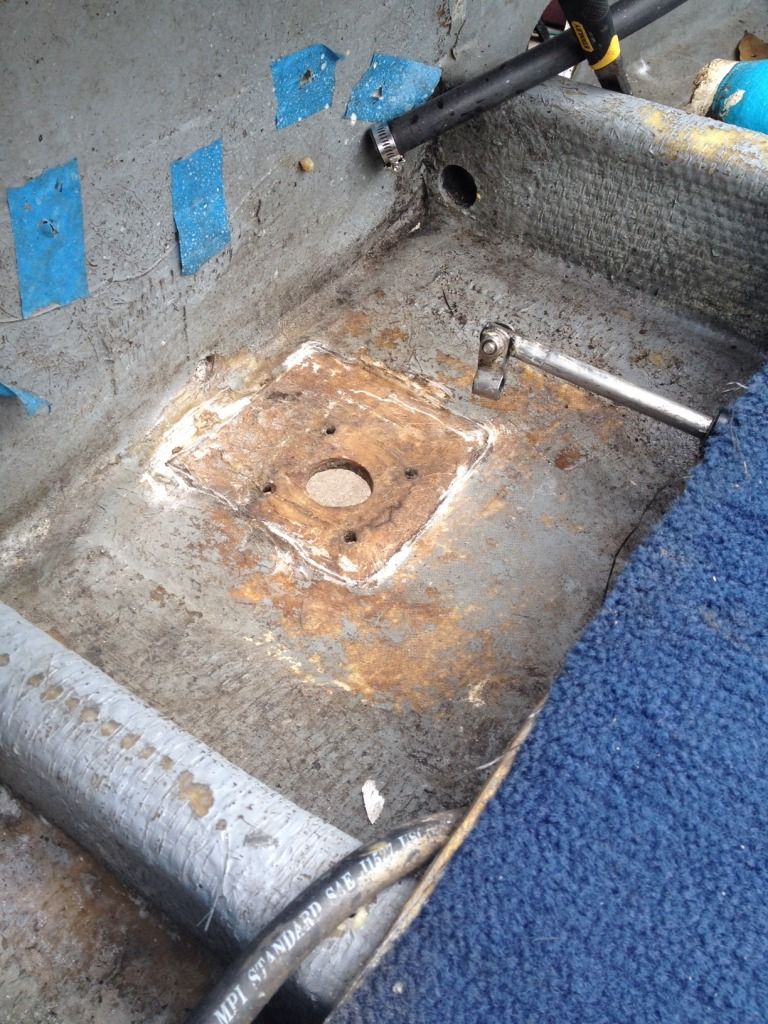
Any help would be greatly appreciated!! Thanks!
Last edited: