Faztbullet
Supreme Mariner
- Joined
- Mar 2, 2008
- Messages
- 15,920
This is why you should use the factory tester as it has no rubber hose to expand and reduce reading.
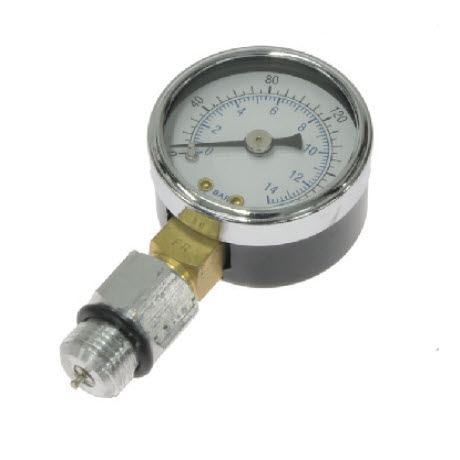
Well, I'd venture a wild guess. Wondering if it might involve crankcase volume? The V6 being a little larger.Well I'm glad we got this ironed out. Glad to have multiparticipants on here to get it right. Certainly helps the guy asking the question sense he deserves the correct answer.
Course my inquisitive mind is asking one final question....why is the V6 compression passing the bar at a 10# lower pressure than an inline?
On the factory tester, I guess you just use a rt. angle adapter for lower and some older top cylinders where the cowling gets in the way.
I started reading through that, until I realized it had so many pages, and any one of them might contain the point you're making. Now thinking maybe I wasn't clear on my point. The difference in volume I'm talking about is as supplied by the original design. Not "what it could be" in the hands of somebody looking to build a race engine. Clearly there are countless way to modify volume, and the trouble to do so, if taken beyond a point, may provide for diminishing returns.Not quite...
Crankcase compression for experts
1. How important is crankcase compression to performance & at what RPM is the increase most beneficial? 2. If crankcase compression help significantly, has anyone tried welding a plate to the bottom of the piston, sealed of course, at this would remove several cubic inches of crankcase volume...www.screamandfly.com
On exhaust timing, thinking back to the Evinrude Triump looper engine and their selecting 3 cylinders because the exhaust pulses used to make the loop work were timed just right, and that being the reason (one of the reasons) for the late arrival of the OMC V4 cylinder engines to the looping process, the first V6s were 2 ea. 3 cylinders hooked to one crank shaft...to get the loop timing right as I read at the time.I started reading through that, until I realized it had so many pages, and any one of them might contain the point you're making. Now thinking maybe I wasn't clear on my point. The difference in volume I'm talking about is as supplied by the original design. Not "what it could be" in the hands of somebody looking to build a race engine. Clearly there are countless way to modify volume, and the trouble to do so, if taken beyond a point, may provide for diminishing returns.
There's also a lot of wandering off point going into exhaust design and comparing the benefits of that vs. crankcase volume issues.
In my mind, trying to keep the V6 (or V anything) crankcase volume as compact as what might be experienced in an inline engine, would be difficult due to the layout of the engine.
And final point, I did say this was a WAG.
Again, the point is being mixed with other info. One more shot and I'm done. ALL ELSE BEING EQUAL, when it comes to the factory suggested compression numbers ("why is the V6 compression passing the bar at a 10# lower pressure than an inline") my WAG would have to do with the difference in crankcase volumes of the V6 vs. the inline engine....As you posted, less crankcase volume increase's crankcase pressure. Simply this speeds up the cylinder filling process but it will not add much to compression overall due to port timing as a lot blows out exhaust. Built several I6"s that would give a V-6 a run for its money. The only thing that holds a I6 back is the reeds cages as they restrict CFM. Put a T2X intake and crank on in one and easy 160HP and a lil porting it will push 190HP
The OMC v6s can sit around 90 psi and be a healthy motor. And that's not even getting into decompression holes. So no the 100 psi rule is kinda outdated.I’d think you’d need to be over 100 to be acceptable on health. I know my old 2.0 V6 2 stroke is around 118-120 psi on a calibrated gauge. That would be at the strong end of things I’d think.
But I’d say we are talking specifically perhaps. Also I’d admit, you’ll be right about other engines too though !The OMC v6s can sit around 90 psi and be a healthy motor. And that's not even getting into decompression holes. So no the 100 psi rule is kinda outdated.