Maybe someone has already figured this out, but it was one of those "eureka" moments and I was too excited at it actually working to not share.
If you have one of the engine alignment tools that requires drilling a 3/8" hole through the alignment tool to use the gimbal bearing driver (such as those sold by MBS Manufacturing as well as others on Amazon/eBay) but don't have the tools or equipment to drill a straight 3/8" hole through a 1 5/16" steel round bar, there is a workaround...
I only have a small bench top drill press and knew that drilling the tool with that was going to be a joke... I do have a friend with machine tools, but I didn't want to tie up his time and break all of his drill bits, and I started thinking - what if I were to use a piece of pipe to hit the driver "puck"?
I actually had a piece of 1 1/2" schedule 80 steel pipe in my scrap pile. I cut a section long enough so that when the tool was seated in the coupler and the driver was seated against the bearing, the end of the pipe would extend just beyond the end of the alignment tool (ended up being 18" or something). After freezing the new bearing for a few hours, I greased the bearing housing, placed the driver tool on the alignment tool, followed by the new bearing. I inserted the end of the alignment tool in the coupler on the engine, set the bearing against the housing and gave the driver a tap with the pipe - it started in pretty easily. I then gave it about 5-6 good smacks with the pipe, using it like a slide hammer, and the new bearing was seated.
Getting machine work done can be expensive and often long lead, so hopefully this saves someone some headaches. If you don't have a piece of 1.5" pipe laying around, I believe some Lowe's sell pipe of this size. You could also hit up a plumbing supply place, like a Ferguson or Hajoca and ask if they have some "drop". I'd imagine 1.5" rigid conduit would work as well, so electrical supply houses are probably fair game as well (and may be able to had at HD/Lowe's). It may not be the best solution for everyone (weighing pricing and availability of the pipe you would need vs availability and pricing of machining services), but it's an option I thought I would share. Also the usual caveat that this should be attempted at your own risk, if your bearing housing is badly corroded or you had to use a D9 dozer to remove the old bearing this may not be the best option, etc....
Anyway, posting this here in hopes it helps someone in the future.
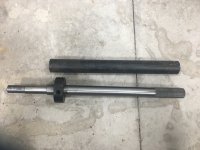
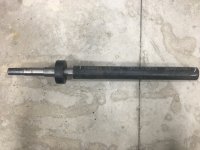
If you have one of the engine alignment tools that requires drilling a 3/8" hole through the alignment tool to use the gimbal bearing driver (such as those sold by MBS Manufacturing as well as others on Amazon/eBay) but don't have the tools or equipment to drill a straight 3/8" hole through a 1 5/16" steel round bar, there is a workaround...
I only have a small bench top drill press and knew that drilling the tool with that was going to be a joke... I do have a friend with machine tools, but I didn't want to tie up his time and break all of his drill bits, and I started thinking - what if I were to use a piece of pipe to hit the driver "puck"?
I actually had a piece of 1 1/2" schedule 80 steel pipe in my scrap pile. I cut a section long enough so that when the tool was seated in the coupler and the driver was seated against the bearing, the end of the pipe would extend just beyond the end of the alignment tool (ended up being 18" or something). After freezing the new bearing for a few hours, I greased the bearing housing, placed the driver tool on the alignment tool, followed by the new bearing. I inserted the end of the alignment tool in the coupler on the engine, set the bearing against the housing and gave the driver a tap with the pipe - it started in pretty easily. I then gave it about 5-6 good smacks with the pipe, using it like a slide hammer, and the new bearing was seated.
Getting machine work done can be expensive and often long lead, so hopefully this saves someone some headaches. If you don't have a piece of 1.5" pipe laying around, I believe some Lowe's sell pipe of this size. You could also hit up a plumbing supply place, like a Ferguson or Hajoca and ask if they have some "drop". I'd imagine 1.5" rigid conduit would work as well, so electrical supply houses are probably fair game as well (and may be able to had at HD/Lowe's). It may not be the best solution for everyone (weighing pricing and availability of the pipe you would need vs availability and pricing of machining services), but it's an option I thought I would share. Also the usual caveat that this should be attempted at your own risk, if your bearing housing is badly corroded or you had to use a D9 dozer to remove the old bearing this may not be the best option, etc....
Anyway, posting this here in hopes it helps someone in the future.
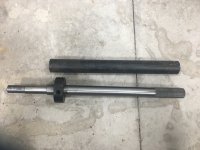
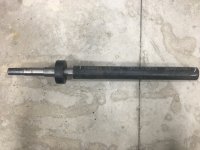