sutor623
Rear Admiral
- Joined
- May 23, 2011
- Messages
- 4,089
$7 piece of steel angle iron.
I have seen a few of these on here. Just thought Id share mine. Downside is you'll need something to cut steel, drill steel, and weld it. I have an old chop saw that I leave a metal cutting blade on and I have used it countless times. Vise holds everything so that I can drill it, and small (70 amp) arc welder that I bought a ways back for $135.
I used an impact gun to get the nut off. Main reason I needed this tool was to be able to torque the nut back on legitimately. I used small (1") bolts down into the flywheel over the puller but couldnt find them for pics....
I have seen a few of these on here. Just thought Id share mine. Downside is you'll need something to cut steel, drill steel, and weld it. I have an old chop saw that I leave a metal cutting blade on and I have used it countless times. Vise holds everything so that I can drill it, and small (70 amp) arc welder that I bought a ways back for $135.
I used an impact gun to get the nut off. Main reason I needed this tool was to be able to torque the nut back on legitimately. I used small (1") bolts down into the flywheel over the puller but couldnt find them for pics....
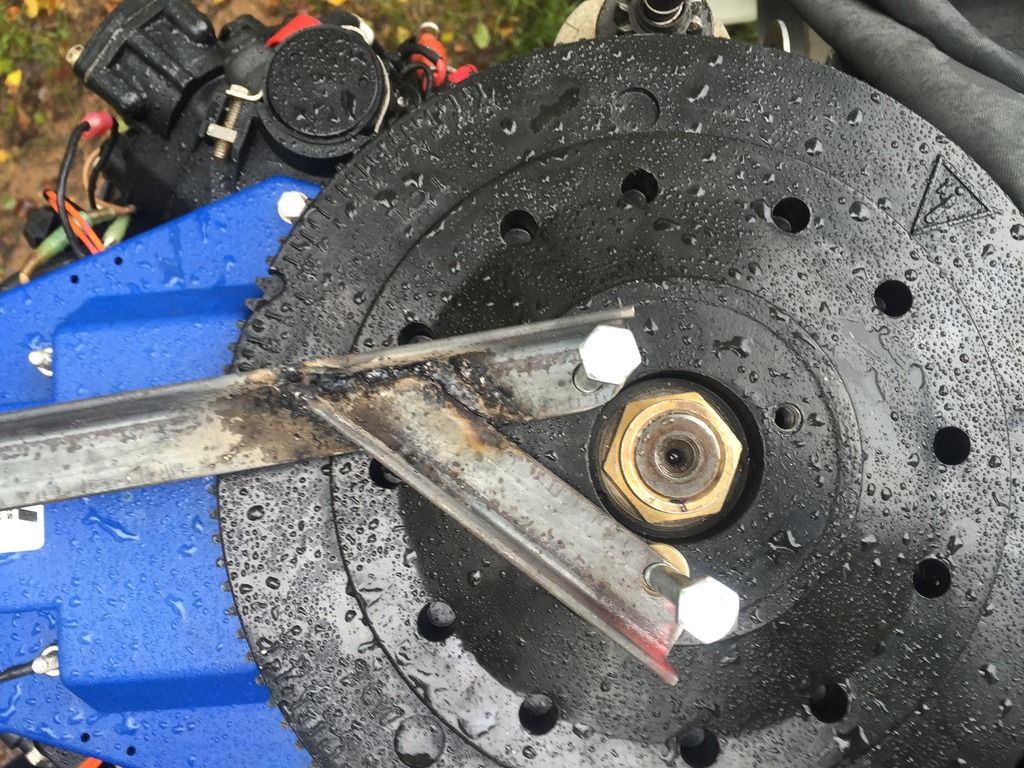
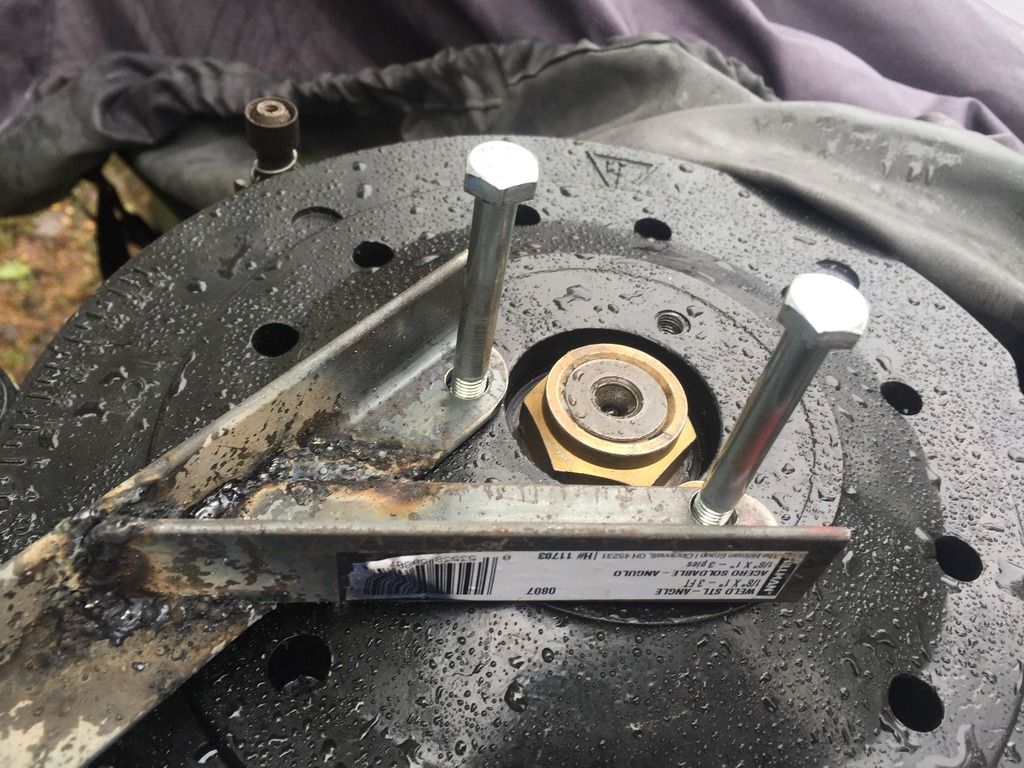
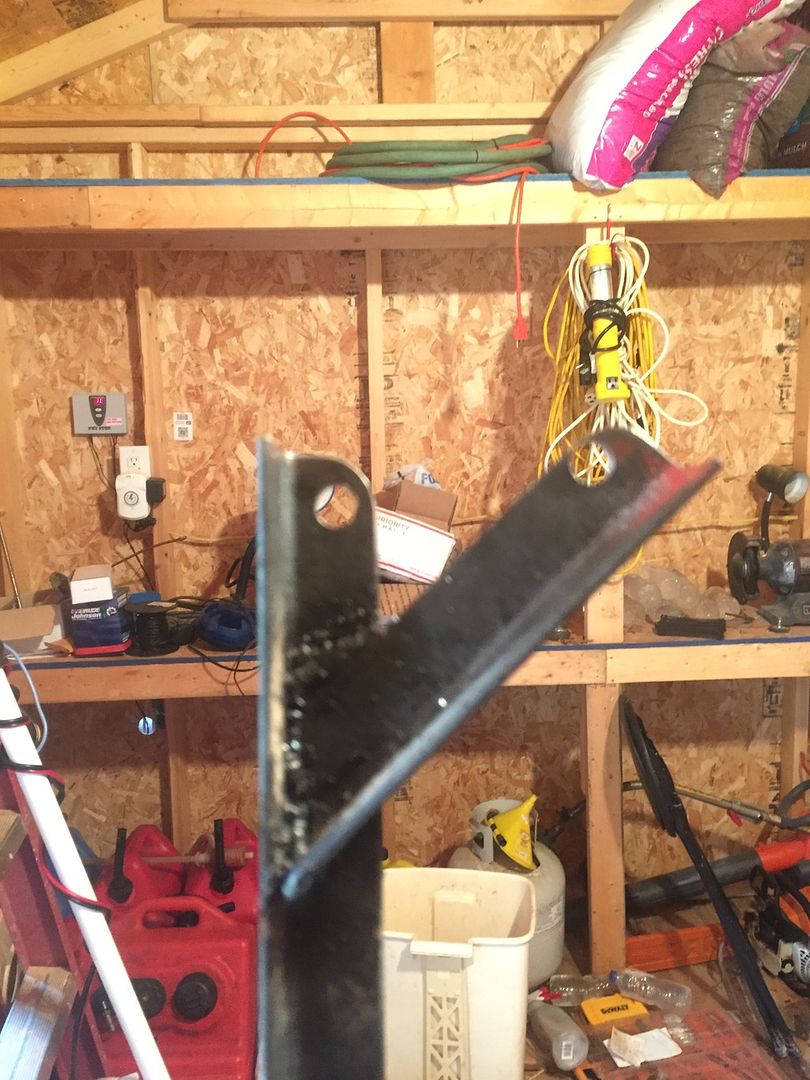
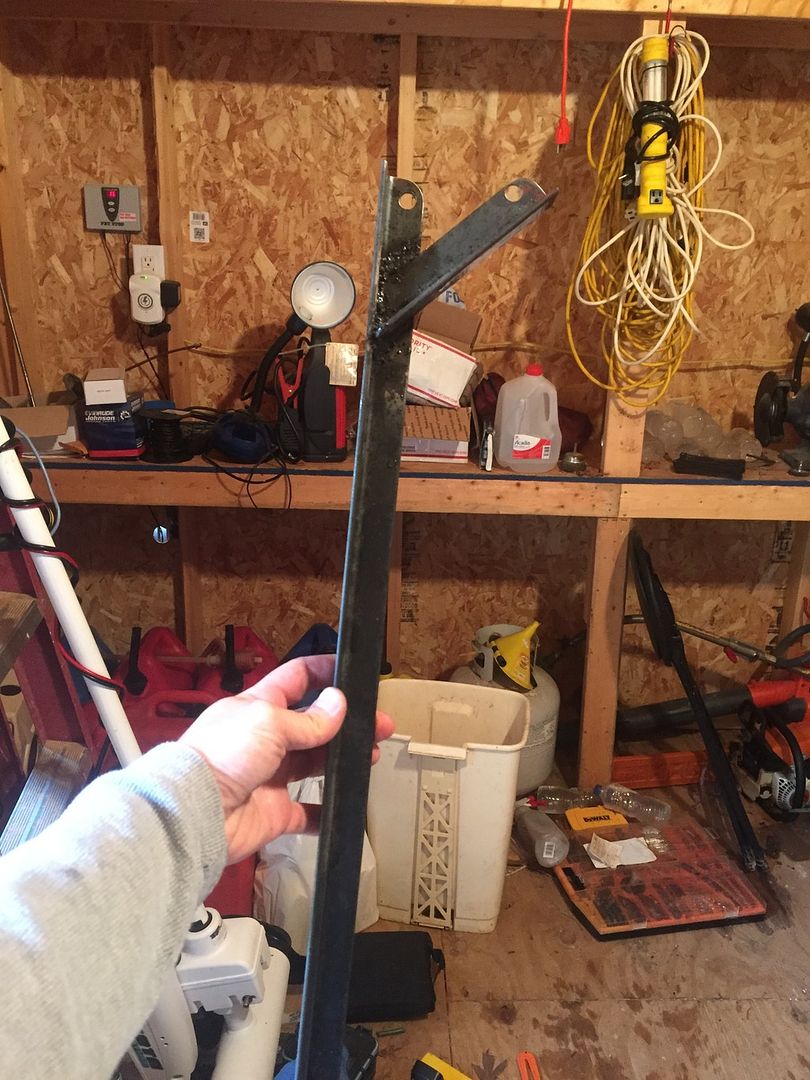