Arawak
Chief Petty Officer
- Joined
- Aug 27, 2010
- Messages
- 486
Grrrrrrr.
Got the harmonic balancer puller today and hooked it up. Tightened it up as much as I could with a ratchet. Pounded on the end with a hammer. Took the propane torch to it. Banged on the flywheel all around with a peice of hardwood. Cursed the #!@$#^% son of a bishop. Fired of the compressor and used the impact wrench to tighten as far as it would go.
So far all I have for my efforts is one of the holes stripped, twice. First time I re-threaded to 7/16" (they were 3/8" to start with). Then the same one stripped again. Dunno if I want to go bigger. Maybe a helicoil?
Maybe dynamite.
Got the harmonic balancer puller today and hooked it up. Tightened it up as much as I could with a ratchet. Pounded on the end with a hammer. Took the propane torch to it. Banged on the flywheel all around with a peice of hardwood. Cursed the #!@$#^% son of a bishop. Fired of the compressor and used the impact wrench to tighten as far as it would go.
So far all I have for my efforts is one of the holes stripped, twice. First time I re-threaded to 7/16" (they were 3/8" to start with). Then the same one stripped again. Dunno if I want to go bigger. Maybe a helicoil?
Maybe dynamite.
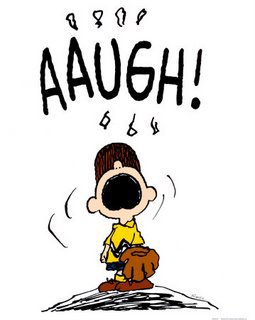
Last edited: