Old Carver
Seaman Apprentice
- Joined
- Dec 12, 2006
- Messages
- 46
Re: OUR CARVER RESTORATION
Been hard at it mock building and drilling all attachment holes the last few weeks,friends from the net,Double Eagle and Hiram helped cut and fit the mock build-up of the deckrail,could not have done it without their help,thanks again guys.
Pulpit railing placed and rub rail rough fit to see if curling will take place in the tight corners,we inverted the railing for this applicatoin and did the same on the swim platform to give it a finished appearance as well.
Bollard placed but will be modifying as I would like to mount the planer mast from the top of it as well as incorporate an anchor tie down.The railing was from the OE and the pcv was a cheap way to mock and fit prior to cutting the heavy walled stainless we will be using.
Trying to keep it all proportionate can be aggrevating.
Made the bow area feel significantly larger.
Blends to thedeck pretty well.
Added new shorepower connector,water tap with pressure regulator and stainless antenna mounts to both sides.
The rear deck is starting to shape up.
Opened up the mount on the swim ladder to match the swim platform mount tubes and drilled through all to eliminate the flex that occured with the origional set up.
Added the taffrail that eventually will hold six rod holders per side.
We had this same style stainless tray mounted in the other boat and have roughed in the housing that will bolt to the deck at this point.Sure makes it easier to work baits and fish.
The panel behind the engine cover cut and access doors are fit.
Will house rod holders and a latch to allow easy access to the batteries.
The panels lay up against aluminum angle finished with a bulb type seal to keep a heavy gulp of water contained to the self-bailing cockpit.
Laid in inner transom plate to check fit and obtain the best cable routing.
Been hard at it mock building and drilling all attachment holes the last few weeks,friends from the net,Double Eagle and Hiram helped cut and fit the mock build-up of the deckrail,could not have done it without their help,thanks again guys.
Pulpit railing placed and rub rail rough fit to see if curling will take place in the tight corners,we inverted the railing for this applicatoin and did the same on the swim platform to give it a finished appearance as well.
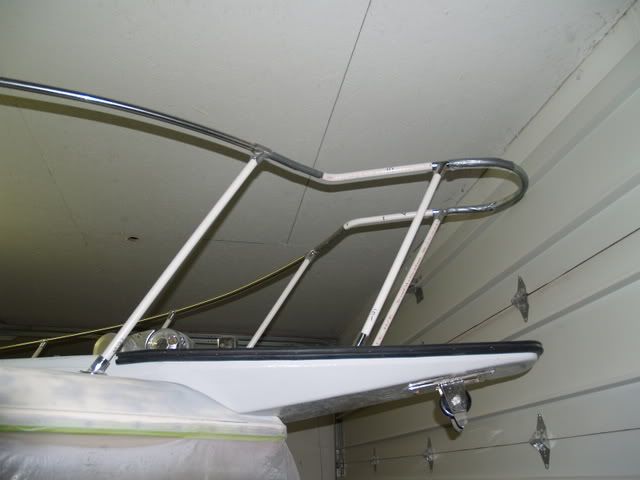
Bollard placed but will be modifying as I would like to mount the planer mast from the top of it as well as incorporate an anchor tie down.The railing was from the OE and the pcv was a cheap way to mock and fit prior to cutting the heavy walled stainless we will be using.
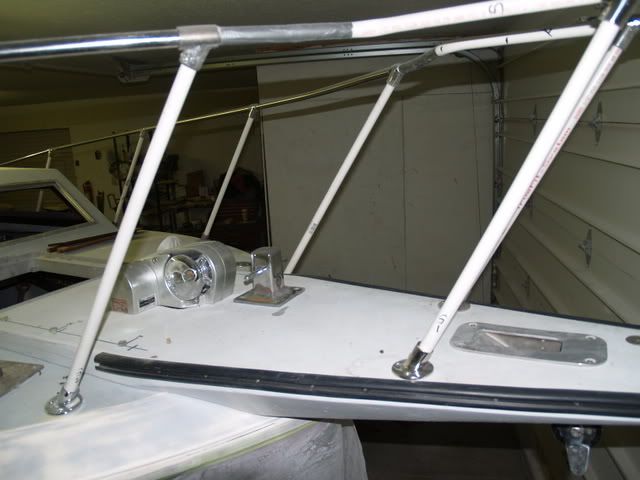
Trying to keep it all proportionate can be aggrevating.
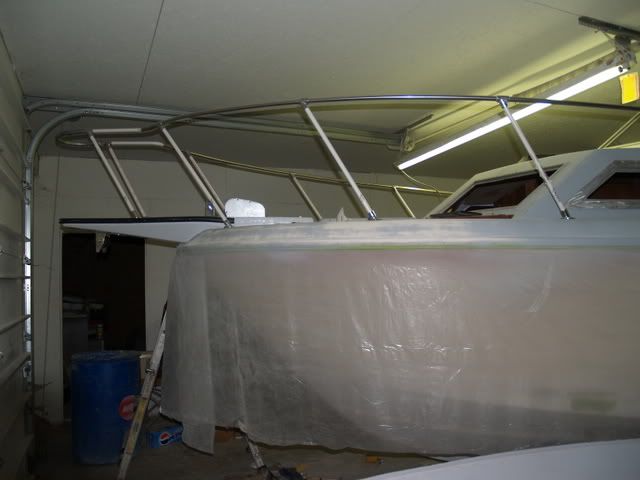
Made the bow area feel significantly larger.
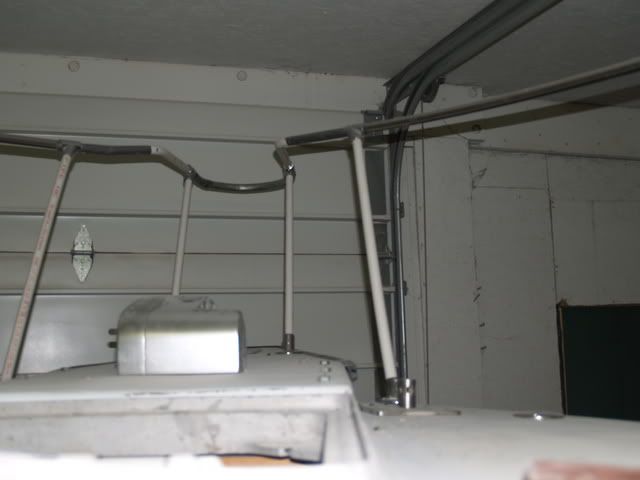
Blends to thedeck pretty well.
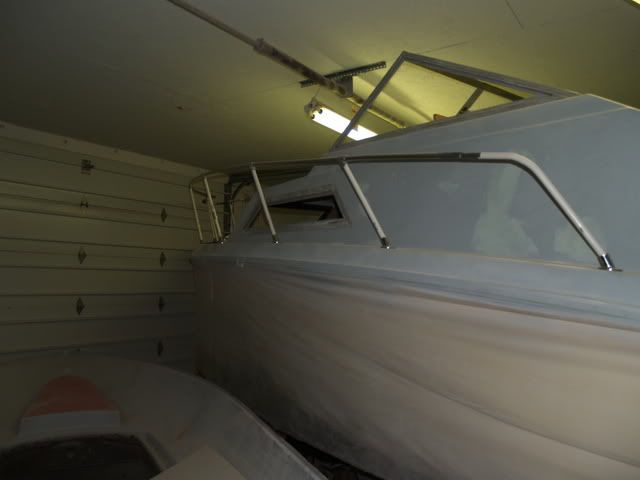
Added new shorepower connector,water tap with pressure regulator and stainless antenna mounts to both sides.
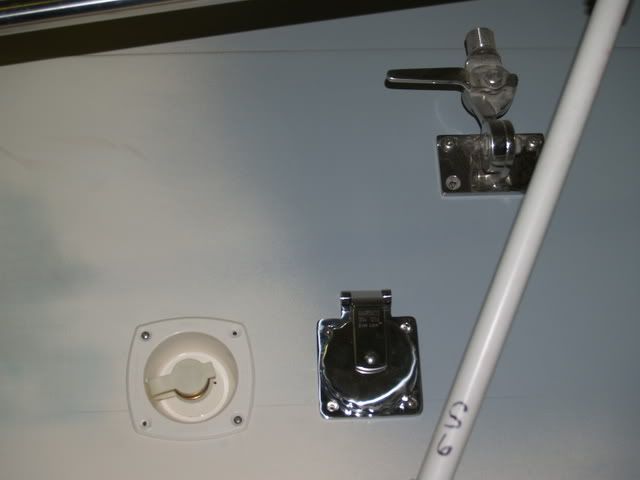
The rear deck is starting to shape up.
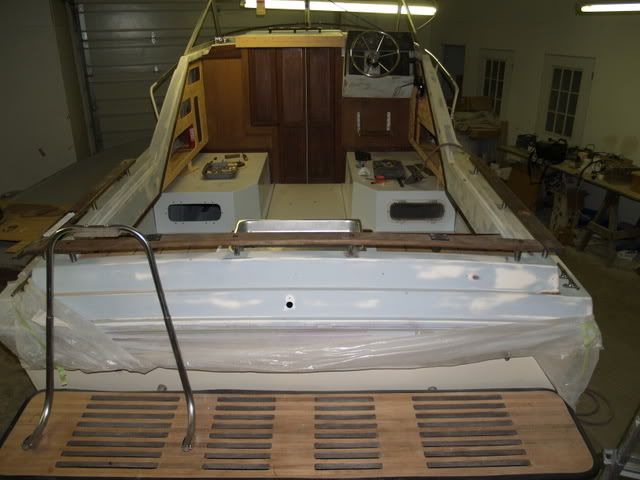
Opened up the mount on the swim ladder to match the swim platform mount tubes and drilled through all to eliminate the flex that occured with the origional set up.
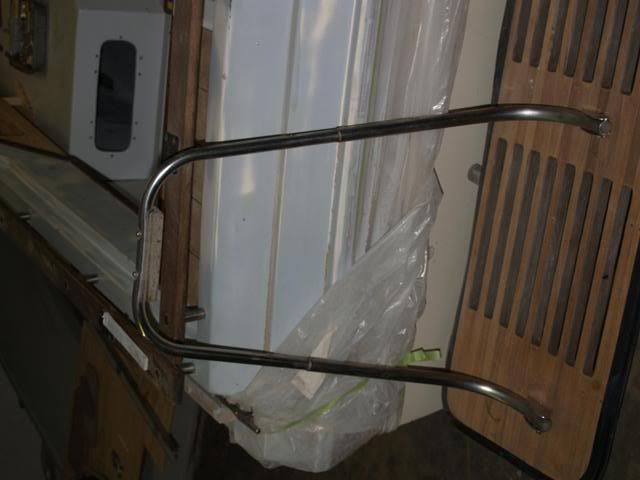
Added the taffrail that eventually will hold six rod holders per side.
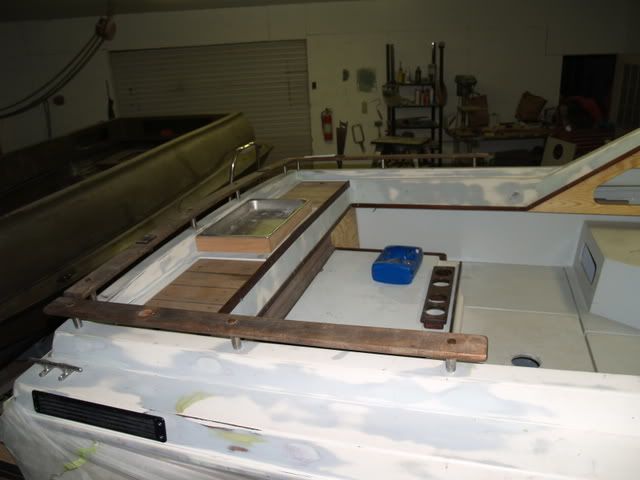
We had this same style stainless tray mounted in the other boat and have roughed in the housing that will bolt to the deck at this point.Sure makes it easier to work baits and fish.
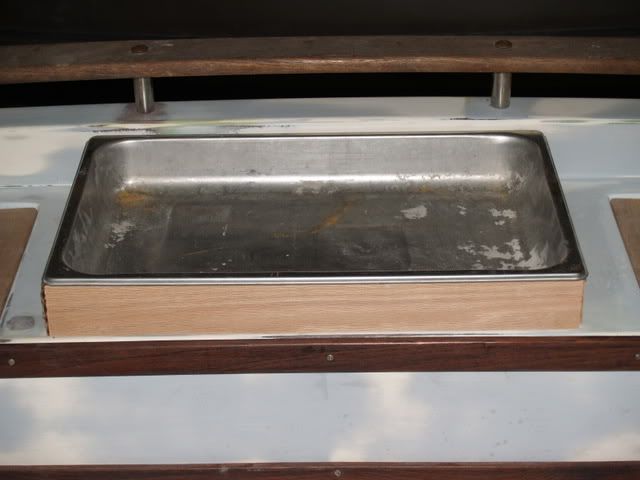
The panel behind the engine cover cut and access doors are fit.
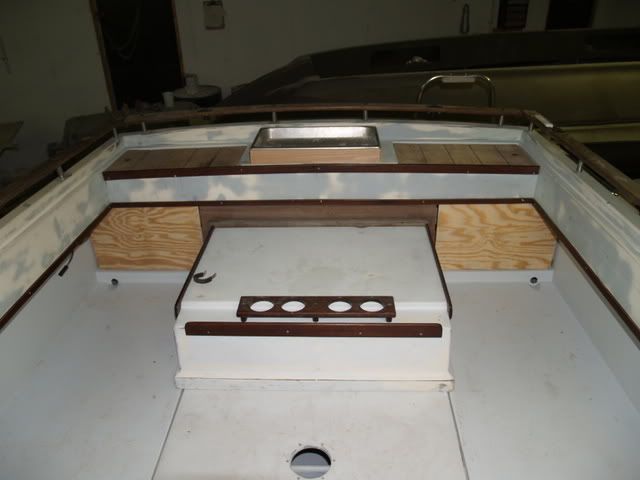
Will house rod holders and a latch to allow easy access to the batteries.
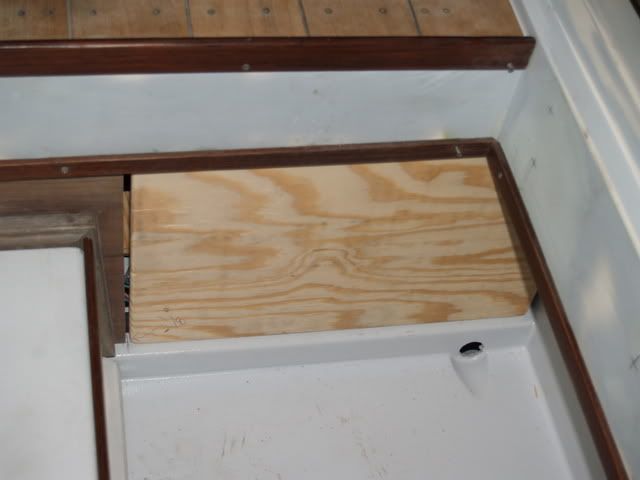
The panels lay up against aluminum angle finished with a bulb type seal to keep a heavy gulp of water contained to the self-bailing cockpit.
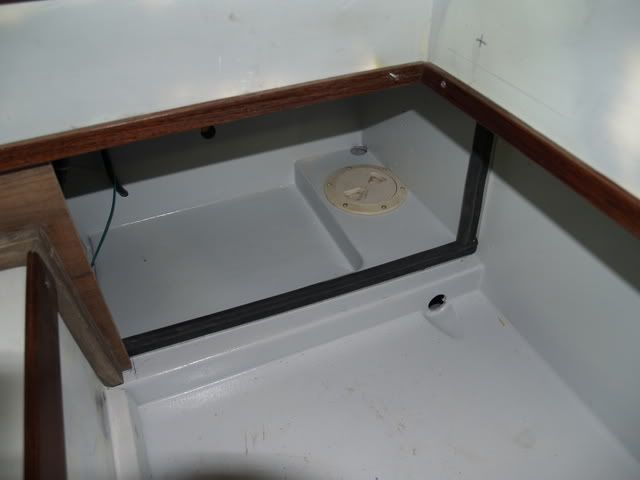
Laid in inner transom plate to check fit and obtain the best cable routing.
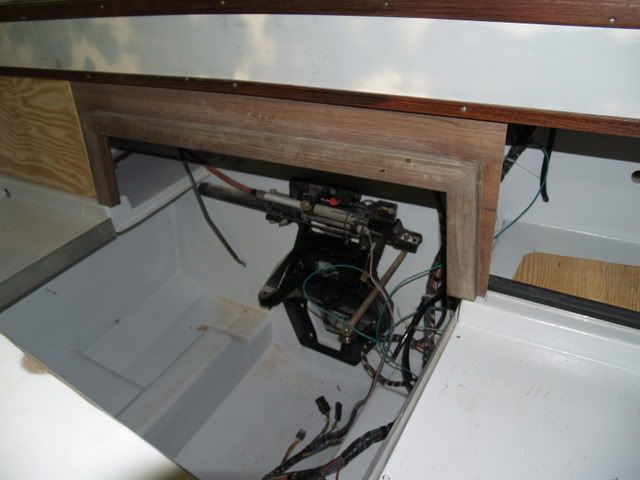