soggystringer
Cadet
- Joined
- Dec 10, 2014
- Messages
- 22
Cheers Rick. and thanks for the advice again wood. Only issue is my 12" roll turned out to only be 8". Not sure where I got 12" from to begin with....
ok got the transom all done yesterday. after PB'ing all the edges and gaps, I put down a layer of 1.5 CSM, then a layer of this weave I have then another 1.5 over the top. I then laid a 1.5 oz over the whole transom to lock it in and seal off the timber. I did put one layer of this weave along the bottom as well. That is where the trim plate will mount to underneath, so now I have to lay some ply there and glass it up when I do the stringers (along with the skeg plate that sits in front of it) This way I figured the transom is solid to the bottom of the hull across there, then the ply goes over which will be glassed in anyway, so strong as.
The weave I bought was out of a bargain bin at my supplier, and it has a pretty dirty the top edge from where it obviously had sat on a shelf for a while, but for $10 I grabbed it. The only thing is it's an 8" wide roll....I thought it was 12" for some reason. Is the tabbing I have done wide enough around the sides? Now's the time to find out!
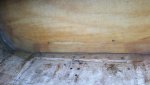
Any guess as to what weight the cloth might be? it's a double bias I think? It has a 45 weave on the other side side too. It's not bad to lay up but it did get a bit tricky in some sections, but managed to get a solid layup.
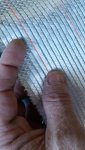
Just a pic showing the bond I got between the new transom and the skin
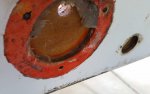
ok got the transom all done yesterday. after PB'ing all the edges and gaps, I put down a layer of 1.5 CSM, then a layer of this weave I have then another 1.5 over the top. I then laid a 1.5 oz over the whole transom to lock it in and seal off the timber. I did put one layer of this weave along the bottom as well. That is where the trim plate will mount to underneath, so now I have to lay some ply there and glass it up when I do the stringers (along with the skeg plate that sits in front of it) This way I figured the transom is solid to the bottom of the hull across there, then the ply goes over which will be glassed in anyway, so strong as.
The weave I bought was out of a bargain bin at my supplier, and it has a pretty dirty the top edge from where it obviously had sat on a shelf for a while, but for $10 I grabbed it. The only thing is it's an 8" wide roll....I thought it was 12" for some reason. Is the tabbing I have done wide enough around the sides? Now's the time to find out!
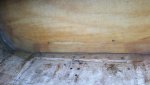
Any guess as to what weight the cloth might be? it's a double bias I think? It has a 45 weave on the other side side too. It's not bad to lay up but it did get a bit tricky in some sections, but managed to get a solid layup.
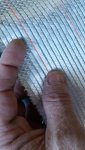
Just a pic showing the bond I got between the new transom and the skin
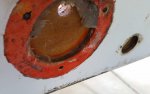
Attachments
Last edited: