Propellerhead
Petty Officer 3rd Class
- Joined
- Nov 15, 2013
- Messages
- 94
Well, it's been a year and a half, so I thought I'd write an update. First of all, I need to admit that I cheated. I was making great progress, and then it all halted. I think that I burned myself out, especially on all that fiberglass work. I was really dreading going in and finishing it all, plus in that time, i got a new job, moved twice, and life just got in the way. I needed a way to get my motivation back, so I farmed out the remainder of the fiberglass on the stringers and engine compartment. There's a fiberglass boat repair shop that's literally a half a block from the hangar. I admit defeat! But you know, it definitely worked to get me motivated again, so I guess I shouldn't feel to bad, right? Here's how it turned out:
It's great to see it in the light of day again.
All the holes from various fittings and the windshield fairing have been repaired and filled.
The exterior transom has been repaired and filled.
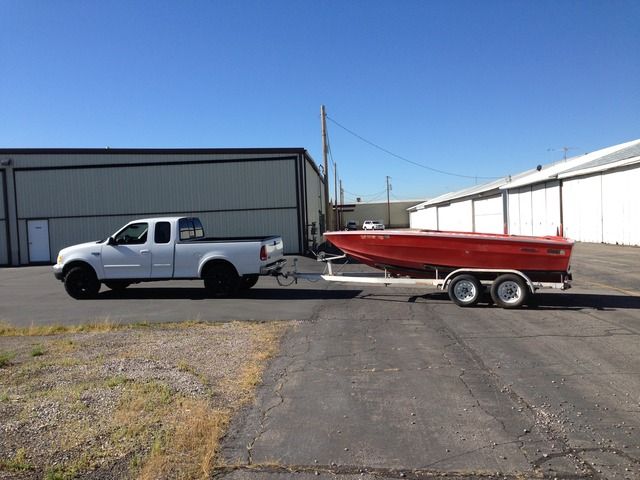
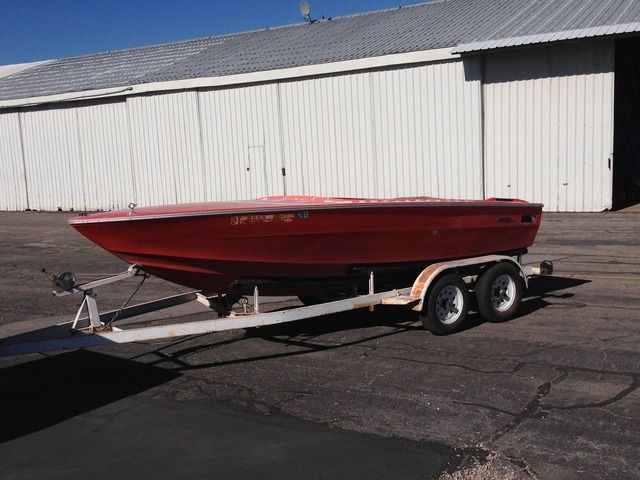
It's great to see it in the light of day again.

All the holes from various fittings and the windshield fairing have been repaired and filled.
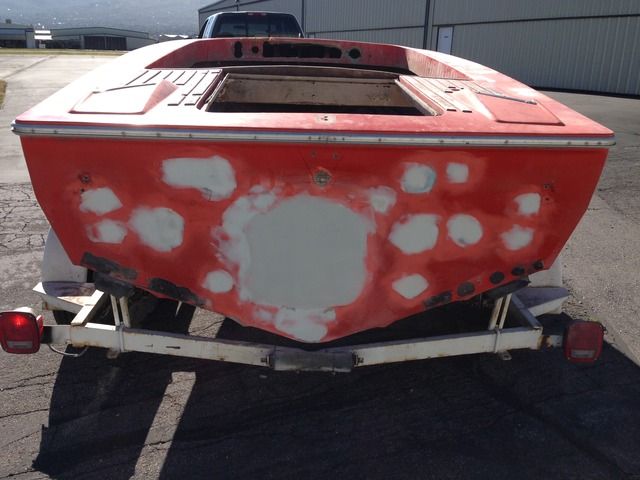
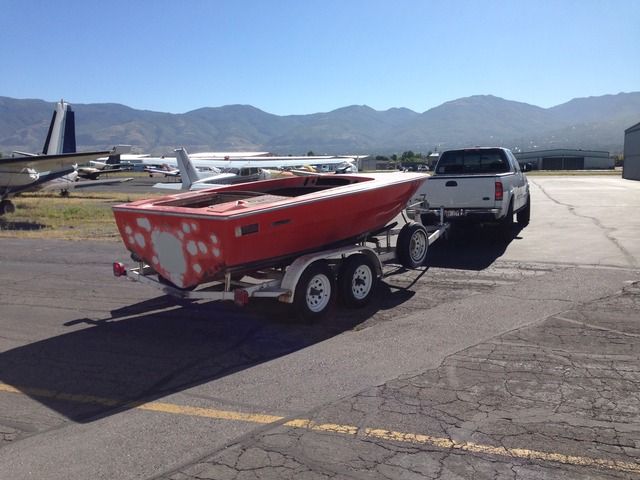
The exterior transom has been repaired and filled.